Spring element connection
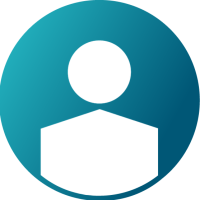
I am simulating a drop test for the landing gear system using Radioss.
The landing gear consists of a tire, a damper, and an arm.
I used a type 4 spring for the damper and used RBE3 for connection to the damper.
After simulating, the connection of the damper and spring element starts to bend.
As can be seen in the picture, the left side is the start and the right side is after the impact.
The pictures show that after impact, the damper connections are no longer parallel.
This problem did not happen to me before and I followed exact same step before.
Why the connection does not work properly?
I am attaching the file I created. Thank you for your help!
Best Answer
-
Spring Type 4 is a single DOF (axial only) spring, it has no bending stiffness, so the behaviour you see is expected
In the attached, I switched them for Spring Type 13 (6 DOF) instead, duplicating your axial properties across and added high bending stiffness
Also, you should not connect anything to the main node of the RBODYs, so I switched the spring connections to a secondary node (and straightened your springs up), I also swapped out your RBE2 between arm and upper damper for another RBODY.
Finally, I had to remesh your 'wheel' component again as it again had very tiny collapsed tetras in it that were causing stability problems
1
Answers
-
Spring Type 4 is a single DOF (axial only) spring, it has no bending stiffness, so the behaviour you see is expected
In the attached, I switched them for Spring Type 13 (6 DOF) instead, duplicating your axial properties across and added high bending stiffness
Also, you should not connect anything to the main node of the RBODYs, so I switched the spring connections to a secondary node (and straightened your springs up), I also swapped out your RBE2 between arm and upper damper for another RBODY.
Finally, I had to remesh your 'wheel' component again as it again had very tiny collapsed tetras in it that were causing stability problems
1 -
Paul Sharp_21301 said:
Spring Type 4 is a single DOF (axial only) spring, it has no bending stiffness, so the behaviour you see is expected
In the attached, I switched them for Spring Type 13 (6 DOF) instead, duplicating your axial properties across and added high bending stiffness
Also, you should not connect anything to the main node of the RBODYs, so I switched the spring connections to a secondary node (and straightened your springs up), I also swapped out your RBE2 between arm and upper damper for another RBODY.
Finally, I had to remesh your 'wheel' component again as it again had very tiny collapsed tetras in it that were causing stability problems
Thank you so much for your help! This is the old model and I was trying to figure out why it starts to bend at the connection point.
So Type 4 has no bending stiffness at the connection point?
Another question is what is the unit of the stiffness K1 and damping C1 when the used unit is kg, mm, ms, kN. For example, if I wanted to have 1kN/mm do I just put K1 as "1", or do I put "1000"?
0 -
Yes, nominally, units are per your input, so if you are using kg, mm, ms, kN, then '1' is 1 kN/mm
however, in your original set up (and I duplicated this in the type13 springs), you had also set the flag 'ileng=1' (spring input defined per unit length) so in this case, the stiffness and damping of your springs are divided by the length (78mm), you had K set at 100, so the stiffness would be 100/78 kN/mm (around 1.28 kN/mm)
This 'per length' will also affect mass, you had 10, so.. 10*78 =780 kg (per spring!)
If you just want to set the stiffness,damping,mass directly, you can use ileng = 0 instead
below from help is what you get with ileng = 1
1