Error ID 205 and 207
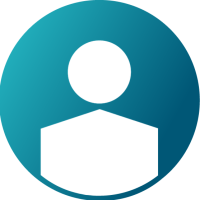
I am currently running a landing gear drop test simulation. The computation stops due to having a mass and energy error after few cycles.
According to the forum I checked penetration and type 7 contact setting, however, did not solve the issue.
What could be the reasons why the simulation stops?
I am attaching the file for your inspection.
Thank you for your help!
Best Answer
-
I took a quick look, there are 2 or 3 issues I think, 1st the mesh on the 'wheel' part is self intersecting/corrupted in a couple (at least) areas which is causing an instability (see below). 2nd The gap sizes on your type 7 (gapmin 0.01, gapmax 0.05) are really too small for it to work correctly. And 3rd your pressures for the tyre are 1000 x too high I think (assuming you are in kg mm ms, pressure is GPa, so atmospheric should be 1e-4, not 1e-1) this was causing your tyre to inflate very rapidly and collide with the structure then become distorted.
I remeshed the bracket, modified contact gaps to 0.5 min, 5.0 max, and changed the tyre pressures to 0.001 pext and 0.003 pini), my modified version is attached
It seems to set off running more happily then. I noted you are using elastic materials everywhere though, so damage etc won't occur and you may see instabilities in the run from using elastic material.
1
Answers
-
I took a quick look, there are 2 or 3 issues I think, 1st the mesh on the 'wheel' part is self intersecting/corrupted in a couple (at least) areas which is causing an instability (see below). 2nd The gap sizes on your type 7 (gapmin 0.01, gapmax 0.05) are really too small for it to work correctly. And 3rd your pressures for the tyre are 1000 x too high I think (assuming you are in kg mm ms, pressure is GPa, so atmospheric should be 1e-4, not 1e-1) this was causing your tyre to inflate very rapidly and collide with the structure then become distorted.
I remeshed the bracket, modified contact gaps to 0.5 min, 5.0 max, and changed the tyre pressures to 0.001 pext and 0.003 pini), my modified version is attached
It seems to set off running more happily then. I noted you are using elastic materials everywhere though, so damage etc won't occur and you may see instabilities in the run from using elastic material.
1 -
Paul Sharp_21301 said:
I took a quick look, there are 2 or 3 issues I think, 1st the mesh on the 'wheel' part is self intersecting/corrupted in a couple (at least) areas which is causing an instability (see below). 2nd The gap sizes on your type 7 (gapmin 0.01, gapmax 0.05) are really too small for it to work correctly. And 3rd your pressures for the tyre are 1000 x too high I think (assuming you are in kg mm ms, pressure is GPa, so atmospheric should be 1e-4, not 1e-1) this was causing your tyre to inflate very rapidly and collide with the structure then become distorted.
I remeshed the bracket, modified contact gaps to 0.5 min, 5.0 max, and changed the tyre pressures to 0.001 pext and 0.003 pini), my modified version is attached
It seems to set off running more happily then. I noted you are using elastic materials everywhere though, so damage etc won't occur and you may see instabilities in the run from using elastic material.
Thank you for your help!
How did you fix the mesh? Did you just meshed it finer or did you use some function to avoid corrupt mesh?
Is it better to have finer mesh than coase mesh to avoid mass and energy error?
0 -
Hi, I first tried a volume tet mesh at an average of 3mm, which is a little finer than you had, I also suppressed some edges (you should be able to see them in the HM file I sent) even with this though there were some poor quality tet elements around the area that had the issue in your model. So I used an alternative approach. I created a tria mesh on the surfaces of the solid part, checked that for small elements and cleaned it up where needed, then I used that tria mesh as the boundary for the tetra mesh. Doing it this way you can control the mesh at the surface more easily. In general, finer is better as it captures the geometry more accurately and means the individual elements should have better quality, but too small in explicit analysis will impact timestep, so there is a compromise to be made, you could go a little bigger than I did, I just went far enough to get it working, (your energy errors were due to the self intersecting elements rather than their size per-se). I should have said before 0.0001GPa (and 0.0003) I had left a 0 out in my message (the model has the correct numbers though)
1 -
Paul Sharp_21301 said:
Hi, I first tried a volume tet mesh at an average of 3mm, which is a little finer than you had, I also suppressed some edges (you should be able to see them in the HM file I sent) even with this though there were some poor quality tet elements around the area that had the issue in your model. So I used an alternative approach. I created a tria mesh on the surfaces of the solid part, checked that for small elements and cleaned it up where needed, then I used that tria mesh as the boundary for the tetra mesh. Doing it this way you can control the mesh at the surface more easily. In general, finer is better as it captures the geometry more accurately and means the individual elements should have better quality, but too small in explicit analysis will impact timestep, so there is a compromise to be made, you could go a little bigger than I did, I just went far enough to get it working, (your energy errors were due to the self intersecting elements rather than their size per-se). I should have said before 0.0001GPa (and 0.0003) I had left a 0 out in my message (the model has the correct numbers though)
Thank you so much for your detailed explanation!
0