Composite Failure
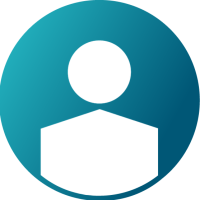
Hi, I made a simple optimization - about composite optimization and steel plate size optimization, the following is the input file, the result shows FEASIBLE DESIGN (ALL CONSTRAINTS SATISFIED).
But when viewing the contour image, it is found that the partial area of the composite is invalid, the composite failure index greater than 1,does it mean that Optimizing the design is not feasible,
Can someone give some advice?Thanks in advance。
Answers
-
Hi @Amasker
For the given objective and constraints, the problem converged and came out as a feasible design.
It is better if you add another constraint of failure index for a better structure.
0 -
Thanks, @Prakash Pagadala
Due to lack of engineering experience, I don't know how to add other constraints to solve this problem. Can you give some advice?
0 -
Like you made a disp constraint, create one more for failure index. You can have multiple constraints.
0 -
Composite failure theory includes Hill theory、Hoffman theory、Tsai-Wu theory、Maximum Strain theory、Hashin criteria
When setting the material properties, choose a failure theory as the composite failure index. As shown below, I don't know how to set multiple failure indexes, or do I understand the failure index incorrectly?
0 -
Hi,
Per PCOMPP you can select only one failure theory.
0 -
Altair Forum User said:
Like you made a disp constraint, create one more for failure index. You can have multiple constraints
Since Per PCOMPP you can select only one failure theory. What do you mean by the above suggestions?,I am confused.
0 -
It is not possible to set multiple failure indices with a single PCOMPP.
If you have used Tsai in PCOMPP, create a composite failure response and select the PCOMPP and use the same as type on the response card.
0 -
Thank you,I try to set composite failure response and failure index constraint,but a fatal error appear:
*** ERROR # 1807 ***
Composite failure responses are applied to ply 1 which belongs to a topology or free-size domain.0 -
Composite failure response cannot be used with topology or freesize.
You can use it with Size optimization.
0 -
because the model deformation and stress are very large, I want to introduce plastic materials, How to define plastic materials in hypermesh, how to set up? Can you give some relevant suggestions or related materials?
thank you
0 -
Altair Forum User said:
because the model deformation and stress are very large, I want to introduce plastic materials, How to define plastic materials in hypermesh, how to set up? Can you give some relevant suggestions or related materials?
thank you
Hi
Is it for isotropic or orthotropic?
If the material is Isotropic, please use MATS1 to include plasticity.
0 -
Altair Forum User said:
Hi
Is it for isotropic or orthotropic?
If the material is Isotropic, please use MATS1 to include plasticity.
I tried to introduce plasticity in MATS1, but the result did not change. Is it wrong with my settings? It seems that plasticity does not work.
Can you check if the model settings are wrong? Thanks
0 -
Hi @Amasker
Linear static analysis will not take plastic data. Please change the analysis type to Non-linear quasi-static, include NLPARM and try again.
0 -
Altair Forum User said:
Linear static analysis will not take plastic data. Please change the analysis type to Non-linear quasi-static, include NLPARM and try again.
Hi, I groped for a day and still don't know how to change the analysis type to Non-linear quasi-static. In addition, I want to introduce plastic properties under static load, and NLPARM settings need to consider load increment. In other words, NLPARM is considering the changing load, but I am applying a constant static load. I am confused about how to set material nonlinearity?. Can I provide some related tutorials or cases? Thank you。
0 -
Hi @Amasker,
you can find how to set up material nonlinearity and solve with NLSTAT analysis:
(tutorial OS-T: 1365 NLSTAT Analysis of Solid Blocks in Contact)
Even though you are applying a constant static load the model should be solved using load increments as there is material nonlinearity- if deformations are excessive then also geometric nonlinearity.
There seem to be unrealistic high forces (total of 1100+ tons of force) acting on a small patch of B-pillar so check the load.
0 -
Altair Forum User said:
There seem to be unrealistic high forces (total of 1100+ tons of force) acting on a small patch of B-pillar so check the load
Thank you very much. @Ivan
At first I wanted to simulate the optimal design of the B-pillar under crash conditions. I didn't find a way to simulate the collision in Optistruct. Because of the simultaneous optimization of composite and the optimization of the size of the steel plate, Radioss cannot be realized at the same time. so use the collision force at 50 km/h is equivalent to static load. Can you give some advice? thanks。
0 -
I am not so sure this optimization cannot be done in Radioss with radopt- have you tried tutorial 51?
Or perform crash test in Radioss and extract maximum contact forces to be used in Optistruct as ESL. The procedure is on page 32:
You can also set up a crash simulation in Optistruct and optimize with ESLM. Please find attached documents.
Your approach IMHO is not the most realistic, because it does not take into account the interaction with other components and crash dynamics.
0 -
Altair Forum User said:
There seem to be unrealistic high forces (total of 1100+ tons of force) acting on a small patch of B-pillar so check the load.
Hi, @Ivan
I calculated the fem file you uploaded and found that after setting the plasticity, the displacement, stress and strain have become very huge. For example, before the plasticity are set, the maximum displacement is 275mm to meet the requirements of the vehicle intrusion, but the stress is very huge.far beyond the limited strength of steel,, but after the introduction of plasticity, the displacement reaches a maximum of 175,000mm. Is this wrong? I'm confused。
0 -
Hi @Amasker Can you share your file with plasticity?
0 -
Altair Forum User said:
I calculated the fem file you uploaded and found that after setting the plasticity, the displacement, stress and strain have become very huge. For example, before the plasticity are set, the maximum displacement is 275mm to meet the requirements of the vehicle intrusion, but the stress is very huge.far beyond the limited strength of steel,, but after the introduction of plasticity, the displacement reaches a maximum of 175,000mm. Is this wrong? I'm confused。
The first file is mine, the plasticity setting is wrong, the plasticity does not work,
The second file is modified by Ivan, the plasticity is set, but the calculation result is unrealistic, and I don’t know where the problem is.
0 -
Altair Forum User said:
I am not so sure this optimization cannot be done in Radioss with radopt- have you tried tutorial 51?
Or perform crash test in Radioss and extract maximum contact forces to be used in Optistruct as ESL. The procedure is on page 32:
You can also set up a crash simulation in Optistruct and optimize with ESLM. Please find attached documents.
Your approach IMHO is not the most realistic, because it does not take into account the interaction with other components and crash dynamics.
@Amasker I ran @Ivan file from the above post as it is and I see normal displacements.
0 -
0
-
Hi,I ran the file again,I found the force is 1000N,but,I intend to convert the collision force of 50Km/h into a static load. The action time is 0.01s, which is about 1300KN, and then spread to the node.
Then I find that the result does not converge. I don't know wether the idea of transforming the collision force into a static load Is feasible。
Here is the file
0 -
the loads are too high and concentrated IMHO.
The assumption of stopping from 50 to 0 kmh in .01s gives 140G which is overly severe to represent real-world collision.
You should first run some simple crash tests to extract the forces involved.
I have performed a side-impact crash test of Metro vs. C2500 @50kmh and the results are presented below. Note the resultant interface force between cars peaks at 160KN and it is distributed to the whole side of the target vehicle.
<?xml version="1.0" encoding="UTF-8"?>
0 -
Hi, @Ivan Thank you very much,
it is unrealistic to find a static load simulation collision. This simulation is even ridiculous. I am now ready to improve the simulation method to convert the static load into a rigid wall collision. After the model was modified, the calculation found that it was an error after a few hours, showing the following information.
*** INTERNAL PROGRAMMING ERROR ***
In file 'datasetFtoC.c', at location # 352.
Can't find the cause of the error? This is my revised file, please check it for me.
At the same time, a simple model was used to simulate the collision. The same calculation time was long. Because of the first use of explicit analysis simulation, some parameters did not know how to set it to shorten the unnecessary calculation time. This is a simple collision file.I am sorry to ask you questions frequently. thank you.
0 -
0
-
0
-
Analysis completed without error. But the error you got is something to with the output.
I think the error is due to CSTRESS and CSTRAIN. Can you remove both and try again?
0 -
Altair Forum User said:
I think the error is due to CSTRESS and CSTRAIN. Can you remove both and try again?
Deselect the CSTRESS and CSTRAIN output. This is still the problem after running the file, will it be related to the time step setting?
0 -
I don't think the problem is with the timestep.
Let me check with the experts.
0