Pload in optistruct and Radioss
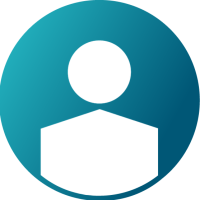

Answers
-
Have a look at Reference manual?
PLOAD = Pressure load
PLOAD1 = load for Rod/beam
PLOAD2 = Pressure load on shell
PLOAD4 = Pressure load on Solid/Shell face
0 -
Hi Vikram,
PLOAD – Static Pressure Load which defines a static pressure load on a triangular or quadrilateral element. It can also be used to define the EXCITEID field (Amplitude “A”) of dynamic loads.
PLOAD1 – Applied Load on CBAR or CBEAM elements, which defines concentrated, uniformly distributed, or linearly distributed applied loads to the CBAR or CBEAM elements at user-chosen points along the axis.
PLOAD2 – Pressure Load on a Two-Dimensional Structural Element. Only QUAD4 or TRIA3 elements may have a pressure load applied to them via this entry.
PLOAD4 – Pressure Loads on Face of Structural Elements.Defines a load on a face of structural elements.
0 -
Hi George,
how can I apply PLOAD4 in Radioss?
0 -
Hi Marta,
In RADIOSS we have only pressure load, which is similar to PLOAD4 in OptiStruct. These keywords are used in OptiStruct.
In Utility Menu>>BCs Manager, select the load type as Pressure Load, select the contact surface of the solid/shell face and user has to define a Pressure vs Time function which has to be recalled in the Curve ID option to apply the pressure load.
0 -
Hi George,
but if I need a function Pressure vs height where pressure is calculate, in accordance with Pascal's Law where
? Is it possible?
Thank you!
Best regards
0 -
Hi Marta,
I don't think its possible as for PLOAD only time function (Pressure vs Time) identifier is available.
0 -
Altair Forum User said:
Hi Marta,
In RADIOSS we have only pressure load, which is similar to PLOAD4 in OptiStruct. These keywords are used in OptiStruct.
In Utility Menu>>BCs Manager, select the load type as Pressure Load, select the contact surface of the solid/shell face and user has to define a Pressure vs Time function which has to be recalled in the Curve ID option to apply the pressure load.
Hi George,
I used this to apply pressure on the Cylinder, however, I can see the results when I solve it by Radioss ( I got normal termination)
when I open the t file to see the animation in the Hyperview it asked me select model reader and result.
0 -
Hi Sara,
For postprocessing the results open the .h3d file or the animation files (A001....) in HyperView. The T01 file is used to create plots and has to be opened in HyperGraph.
I recommend you to remove /DT/NODA/CST card and run this model.
0 -
Dear George,
I simulate a two ends constrained hollow cylinder under pressure load in hypermesh radioss. I did not set any rule for failure. my answer depends on termination time and after a certain time it shows awkward deformation. is it related to do not have failure criteria?
Best Regards,
sara
0 -
Hi Sara,
For your model the thickness defined is very less, .011mm and when the load acts it deforms very badly. I just increased the thickness to 0.5mm and the same .h3d is attached for your reference.
0 -
Altair Forum User said:
Hi Sara,
For your model the thickness defined is very less, .011mm and when the load acts it deforms very badly. I just increased the thickness to 0.5mm and the same .h3d is attached for your reference.
Dear George,
I know that this model is very easy and I should not have a lot of problems at that, but I cannot understand why I have this awkward deformation.
I changed the thickness and also consider all surface of cylinder as my contact surface. However, changing the thickness just increase the termination time. in the previous thickness I saw awkward deformation at termination time=17 now I saw it at about 30.
my model is attached
0 -
Altair Forum User said:
Dear George,
I know that this model is very easy and I should not have a lot of problems at that, but I cannot understand why I have this awkward deformation.
I changed the thickness and also consider all surface of cylinder as my contact surface. However, changing the thickness just increase the termination time. in the previous thickness I saw awkward deformation at termination time=17 now I saw it at about 30.
my model is attached
I mean how can I calculate the right termination time?
Best Regards,
Sara
0 -
Hi Sara,
It seems like this weird behavior is obvious on this model. As mentioned earlier the pipe thickness is very low, constrained both ends and you are applying a pressure load continuously on a surface. In a real life case the pipe will break after a particular time but in this case no rupture or failure parameters were given and the pipe continues to deform which results in a weird behavior.
Normally starting from a zero load, and zero solution, we gradually ramp up the load until we achieve the desired total load. This gradual ramping up the load is often a more robust approach for solving nonlinear problems. And we run these models normally for the time which we ramped the load. If you continue to run the model after the loading time the load will continue to ramp.
You can watch this webinar which provides basic guidelines on applying quasi static loading in explicit analysis: https://altairuniversity.com/learning-library/7-guidelines-to-apply-quasi-static-load-in-explicit-simulation/
0 -
Dear George,
Thank you so much for your help and time.
Best Regards,
Sara
0