Time step for small element size in Radioss
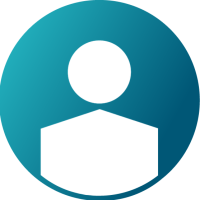

Hello everybody,
I want to perform an explicit analysis in radioss. I have read that we follow a time step of 1E-06 sec for steel with minimum element size of 5 mm. In my case the element size goes up to 1 mm.
I have gone through the book 'Crash Analysis with Radioss', according to which we have to look for two formulae to calculate the time step- one is elemental time step and the other is nodal time step. With an approximate sound speed of 5000 m/s through steel, I calculated the time step of 2E-07 sec [i.e., 1 mm / 5000 m per sec]. But I am not able to figure out how to calculate the nodal time step? Would somebody help me out with this?
My question is - how much smaller time step would I require to take (for steel) in this case? [Please suggest me an optimum- rough estimate for the element size of 1 mm for steel by taking into consideration the nodal time step also].
Answers
-
Hi Amar,
The nodal time step equation is : sqrt (2m/k), where m is nodal mass and k is equivalent nodal stiffness. A scale factor will be also used to calculate the time step.
Please go through https://altairuniversity.com/learning-library/considerations-about-time-step/ which is a webinar showing time step calculation in RADIOSS.
RADIOSS will calculate nodal and elemental time steps of the model and will choose the highest of these to run.
From Check Elems (F10) panel it is possible to determine the approximate minimum time step for explicit solvers based on element dimensions.
0 -
Altair Forum User said:
Hi Amar,
The nodal time step equation is : sqrt (2m/k), where m is nodal mass and k is equivalent nodal stiffness. A scale factor will be also used to calculate the time step.
Please go through https://altairuniversity.com/learning-library/considerations-about-time-step/ which is a webinar showing time step calculation in RADIOSS.
RADIOSS will calculate nodal and elemental time steps of the model and will choose the highest of these to run.
From Check Elems (F10) panel it is possible to determine the approximate minimum time step for explicit solvers based on element dimensions.
Sir, I tried checking time step with Check elements Panel, but an error popped up:- 'HM_CALC_TIMESTEP_func: Division by zero error'
Does the F10 panel calculates considering both the elemental and nodal time steps?
Also, What care we should take to keep the nodal time step maximum?
0 -
Hi Amar,
This seems to be a defect. Please let us know which HyperWorks version are you using?. Is it a Student Edition?
In order to increase the time step, we have following options:
• Increase the element length (Always preferred at least for initial runs)
• Increase the density of the component thereby increasing the mass of component..
Option 2 is called as the “Mass Scaling“. Although this increases the computational speed considerably, care must be taken to see that a bound is put on the percentage of mass increase. Secondly it should not change the physics of the problem i.e. mass increase is allowed for deformable bodies but if applied to rigid bodies then results will be different than the original model.
Also you can use /DT/NODA/CST keyword to control the nodal time step.
0 -
NC= 4500 T= 4.4900E-03 DT= 1.0000E-06 ERR= 0.0% DM/M= 1.1356E+00
ELAPSED TIME= 1237.04 s REMAINING TIME= 1518.03 s
RESTART FILES: saddle_2_0001_[0001-0001].rst WRITTEN
NC= 5000 T= 4.9900E-03 DT= 9.9999E-07 ERR= 0.1% DM/M= 1.1356E+00
ELAPSED TIME= 1379.18 s REMAINING TIME= 1384.68 s
ANIMATION FILE: saddle_2A006 WRITTEN
NC= 5500 T= 5.4900E-03 DT= 1.0000E-06 ERR= 0.1% DM/M= 1.1357E+00
ELAPSED TIME= 1520.82 s REMAINING TIME= 1249.32 s
NC= 6000 T= 5.9900E-03 DT= 1.0000E-06 ERR= 0.1% DM/M= 1.1357E+00
ELAPSED TIME= 1666.80 s REMAINING TIME= 1115.82 s
ANIMATION FILE: saddle_2A007 WRITTEN
NC= 6500 T= 6.4900E-03 DT= 9.9999E-07 ERR= 0.0% DM/M= 1.1357E+00
ELAPSED TIME= 1825.74 s REMAINING TIME= 987.40 sIs it ok ?
0 -
Hi,
This out file seems ok. But the mass added is high. Ideally the mass error should be less than 5%, that is .05. Reduce the imposed time step value in the engine file.
0 -
In one of my simulation ERR values goes to 99 % and then simulation stops what could be the reason for the same ?
0 -
RUN KILLED : ENERGY ERROR LIMIT REACHED
0 -
WARNING ZERO OR NEGATIVE SUB-VOLUME : 3D-ELEMENT ID
0 -
Hi,
There could be several reasons for high energy error. High distortions or deformations happening in the model can lead to such a situations. Also check the model for any penetrations or intersections.
The negative volume issue happens when the solid elements are very deformed and their characteristic length goes to 0. For large strain formulation the time step of an element goes to 0 when the element is compressed. /DT/BRICK/CST is used in order to prevent the solid elements from negative volume. At those cases in solid property Ismstr =2 is used which will use large strain formulation while their time step remains greater than Tmin, and will then switch to small strain formulation.
0 -
If the penetration are unavoidable what to do ?
0 -
Is this problem is anywhere related to contact ?
0 -
Hi,
As mentioned before there could be several reasons for high energy error and this could be related to contact. You can check this using the penetration check tool in HyperMesh.
0