3PB Impact Test
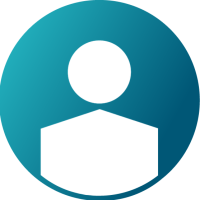

Hi there,
I m trying to validate a 3 point bending simulation using a paper which presents both numerical and experimental data. I followed the exact same setup but the resultant force I keep getting is always 20% smaller than the one pretended. I've double-checked materials, properties, contacts and boundary conditions and nothing seems to change. I've tried the validation process with different papers and I always get the same problem. Any idea on what I might be doing wrong?
Thanks,
Answers
-
Do you try to calculate with different mesh density?
0 -
Yes. I've tried from 6mm characteristic length elements until 1mm and the solution appears to be well converged
0 -
Altair Forum User said:
Yes. I've tried from 6mm characteristic length elements until 1mm and the solution appears to be well converged
You say there're 20% different comparing to experimental results, but that's deformation or stress?
0 -
Applied force over time
0 -
The deformation is imposed by the punch's constant velocity
0 -
-
I've figured it out. I had inertial problems due to poor sizing of the structure. The paper I am using considers the section's characteristic length as the inner dimension (to which you add the thickness) and not the average one. The section I was using was then undersized and therefore the bending force the beam was able to sustain was lower.
Thanks anyway! Using a more refined mesh is helping me reaching a better solution
0 -
Always using a more fine mesh will give a better solution but will increase the solving time. So, keep the best element size which will give good results and meanwhile solves quickly.
0