topology optimization
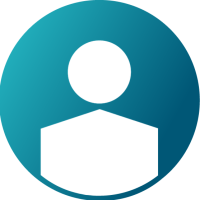

Hello,
I would like to optimize aerospace brackets by performing topology optimization.
The main objective is to keep the natural frequencies of brackets in axial and radial directions less than 240 Hz with minimum mass and satisfying Reserve factor of 1.
There are also static loads applied on the brackets.
The topology optimization methodology, I have chosen was
Minimize combined compliance index, constraint : Frequency > 240 Hz , stress constraint and volume fraction.
Am I going in the right direction?
Also is there any other method to minimize mass considering both static loads (stress constraint) and frequency constraints??
Answers
-
We suggest you to either run a Classical Topology setup as follows;
Minimize Compliance Index (combined Linear Static and Frequency) with Volume Fraction constraint. >> This is stiffness based design (no stress) and only gives you load path directions; ideal for a quick setup and a check for design feasibility and package space.OR
Use Minimize Volume with Stress and Frequency (multiple modes) constraints.
0