Buckling Analysis Composites (PCOMPP)
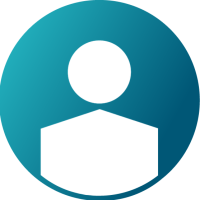

Dear,
I am trying to preform a buckling analysis of a composite sandwich material.
But the Auto-SPC limits the DOF's of the composite skins, so that buckling can not happen in correct way.
When the Auto-SPC is dissabled, the solver gives the error which states that the DOF's of these elements should be limited, because they have no stiffness in that direction.
This is true, due to the material and property assignment (Mat 8, and PCOMPP) which does not provide stiffness in the 3th direction.
Is there a work around?
I also did a dynamic test (Radioss) where the specimen does not buckle according to the first mode.
Test to be replicated:
<?xml version="1.0" encoding="UTF-8"?>
Optistruct First mode
<?xml version="1.0" encoding="UTF-8"?>
Faulty result due to Auto SPC
<?xml version="1.0" encoding="UTF-8"?>
RADIOSS Result
<?xml version="1.0" encoding="UTF-8"?>
Answers
-
Hi,
Can you model the layers with solid elements and use MAT9ORT?
You can use PCOMPLS you model solid layers.
0 -
Altair Forum User said:
Hi,
Can you model the layers with solid elements and use MAT9ORT?
You can use PCOMPLS you model solid layers.
I can do this, but up until now I have refrained from using 3D elements for the modelling of the composite skins because of the error introduced when modelling slender elements using solid elements.
Like is mentioned in the Altair Book 'Practical Aspects of Finite Element Simulation', and in University.
Would this be a large error?
I will try the 3d element method, and report back in a few hours0 -
HI,
I never assessed the error margin for an orthotropic material model.
If you see anything strange, please let us know.
0 -
PCOMPLS is not supported in Buckling analysis
I will try something different using 3D elements
*** ERROR # 4233 ***
Layered solid shell composites (PCOMPLS) is not supported
in buckling analysis.
(There are some other warnings and stuff, but I haven't debugged properly, because using this property will not work for the analysis.)0 -
Hi @ArneDerluyn
Can you try with PSOLID. I think that is the only way to provide stiffness in the thickness direction.
0 -
Okey,
I now have a working model.
But the Modal analysis creates a self-intersecting geometry, which indicates that something is still wrong.
I have assigned different PSOLID properties per ply, by transforming the stiffnesses according to the fibre direction.
This is something which I generally try to avoid because it is a seed for errors.
The model also shows some edge effects.
This model is less strong than the physical test, the model indicates only 72% of force allowed versus the physical test.
Buckling result (Mag x10)
0 -
0
-
how to create a metal and carbon plies in single laminate
0 -
Hi,
You can use MAT1 card for modeling metal and use the same in your laminate.
0