Topology optimization results interpretation
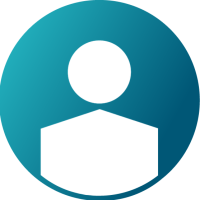

Hi!
I have a question connected with topology optimization results. I optimized solid Design Space, but as the result I got shell structure when I choosen equal values on the result panel.
1) Could you please explain why is this shell and how Optistruct calculates mass in .out file in this case: mass of solid or shell?
2) What is the physical difference between element densities as 0.8 instead of 1?
Best regards
Answers
-
Altair Forum User said:
What is the physical difference between element densities as 0.8 instead of 1?
The penalization technique used is the “power law representation of elasticity properties,” which can be expressed for any solid 3D or 2D element as follows:
K(r) = K*ρ^p
where K and K represent the penalized and the real stiffness matrix of an element, respectively, ρ is the density and p the penalization factor which is always greater than 1.
In OptiStruct, the DISCRETE parameter corresponds to (p - 1). DISCRETE can be defined on the DOPTPRM bulk data entry. P usually takes a value between 2.0 and 4.0. For example, compared to the non-penalized formulation (which is equivalent to p=1) at ρ=0.3, p=2 reduces the stiffness of the element from 0.3 to 0.09 times the stiffness of the fully dense element. The default DISCRETE is 1.0 for shell dominant structures, and 2.0 for solids dominant structures (the dominance is defined by the proportion of number of elements)0 -
You can interpret it as 0 is void and 1 as material availability.
After optimization, the material density may vary between 0 and 1.
0 -
Thank you very much for your advices!
But how can I get a solid structure as a result, not shell? Can I apply some settings to control it?
Best regards
0 -
Hi @Ekaterina
if your model contains solid elements the optimization result will still be based on the same solid elements. The same goes for shell elements. In other words, the element types are not changed by optimization.
In Hyperview use the Iso panel which allows you to display single iso values (iso surfaces for solids or iso line for shells) dependent on results data. Some solids may appear so thin as shells in iso (especially when processed with averaging methods), but they are in fact still solid.
0 -
The problem with your first formulation is conatraints are not respected and all the material is removed.
Start with compliance and volume fraction.
0 -
Thank you very much for your advices!
I have tried to optimize with volume fraction constraint and compliance minimization and have got the following result:
Then I imported the result to HyperMesh by means of OSSmooth. But the structure is still too heavy.
1) Could you please recommend the rational constraint choice sequence in this case?
And also I tried to conduct topology optimization procedure for bigger design space:
But the result structure is not continuous.
2) So how I can get the continuous structure instead of discrete?
Best regards
0 -
Hi,
You can enforce Manufacturing constraints to get a meaningful result and use mass constraint and check if that helps.
0