Optimization of a laminate with a non-symetric core
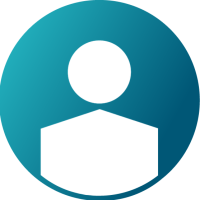

Hey Guys,
I'm trying to modelate what in formula student is called as a groove, this is a place where we take the core and unite the inner and outer layers of the monocoque (image below)
To build my model i followed the steps:
-Import a solid from the CAD, mesh the upper and bottom faces of the solid with a 2D mesh and then a 3D mesh to the solid;
-Changed the upper and lower face to another component to create the plyes, create them and the laminate.
-Create a property PSolid for the laminate and PComPP for the plyes;
-Material for the core is a Mat1 and for the plies a Mat8
-The constraints and forces are in the image below. The force is applied in a rigid at a certain distance of the laminate
The problem is when i run i have a displacement of 1e+10 and i don't understand why
Find more posts tagged with
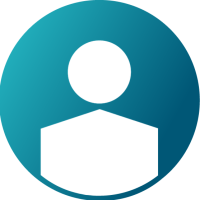

The problem is when i run i have a displacement of 1e+10 and i don't understand why
use nonlinear solver.
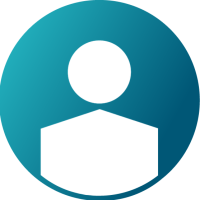

use nonlinear solver.
Hi,
Can you constraint all DoFs and check if that helps?
Thanks for your answers, i already solved the problem. The upper and bottom surface are not well conected. I have another question, what is the better material card for the core since it is an aluminium honeycomb?
I am also interested in taking a force vs displacement curve of this with an increasing force. Is it possible to do in hypermesh? What should i do? Is there anything that i can check that help me doing that?
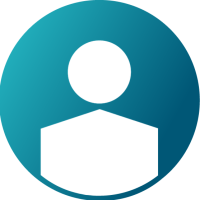

Thanks for your answers, i already solved the problem. The upper and bottom surface are not well conected. I have another question, what is the better material card for the core since it is an aluminium honeycomb?
I am also interested in taking a force vs displacement curve of this with an increasing force. Is it possible to do in hypermesh? What should i do? Is there anything that i can check that help me doing that?
You can model core as just solid and use MAT1 card with PSOLID property.
Force Vs displacement for linear static?
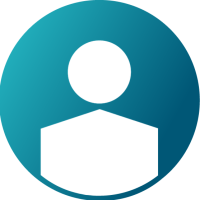

You can model core as just solid and use MAT1 card with PSOLID property.
Force Vs displacement for linear static?
Is what i have done.
My objective is trying to simulate a traction test and obtain the displacement with an increasing force. I think its non linear but i'm not sure
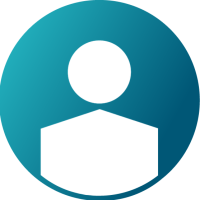

Is what i have done.
My objective is trying to simulate a traction test and obtain the displacement with an increasing force. I think its non linear but i'm not sure
Yeah or transient
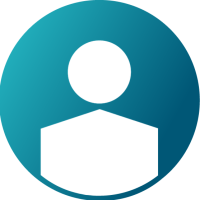

Yeah or transient
What do you think is the best option to do this with altair products (Optistruct or Radioss)
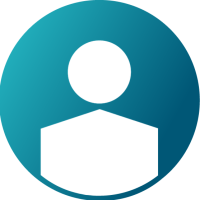
Hi,
force vs displacement curve can be done using non-linear quasi-static analysis (NLSTAT) in Optistruct. There are a few examples:
https://community.altair.com/community?id=community_question&sys_id=804688761b2bd0908017dc61ec4bcb68https://community.altair.com/community?id=community_question&sys_id=8696c07a1b2bd0908017dc61ec4bcbba
Radioss should be used if there are inertial effects due to high loading rate.
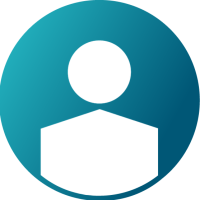

What is considered to be inertial effects? Is like reduction of thickness in some points?
Is it possible to model the honeycomb with the Material P9ORT, because the honeycomb have diferent resistance in compression axis and plane axis (Attached you can see the properties of the honeycomb)
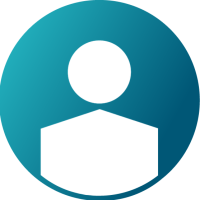
Inertial effects are due to acceleration in dynamic events: we must consider mass (inertia), i.e. sum of all forces = m*a
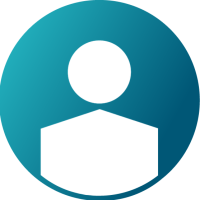

Hi @JFormiga14
You can model with MAT9ORT+ PSOLID/PCOMPLS. As Ivan expressed that Inertia effects are due to accelerations and are considered in dynamic events. So, if you are running a linear static analysis, inertia effects will be ignored.
Hi,
Can you constraint all DoFs and check if that helps?