Interpretation of Weighted Compliance in topology results
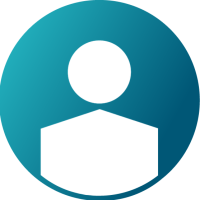
Dear Jan,
Thank you for the feedback on the meeting yesterday. I have a question regarding the weighted compliance that we discussed in the end. I have now tried to use different weighting factors for the different load cases to see how it affects the result. However, I receive the same design regardless of the weight factors I use. So I wonder in what way should the weighting factors affect the new design?
If I have understood it correct the weighted compliance is the weight factor*compliance for load case 1 + weight factor*compliance for load case 2. So you get a new value on the compliance that will be minimized during the optimization, but how does the value of the compliance affect the outcome of the design?
Kind regards
Linn
Answers
-
Dear Linn,
the weighting factor can influence your final design, but it might also happen, that your results remain unchanged with a new weight factor. To have a better understanding, please imagine the following scenarios:
- you have two loadcases, e.g. bending and torsion. The compliance in load case bending is 100 x higher than in load case torsion (due to much higher loading). That means your final topology with objective min. weighted compliance (Weight factor 1 for both load cases) will be determined and driven mainly by the bending load.
- If you now set the weight factor torsion loadcase to 3.0, the design will still remain optimal for bending, as the torsional compliance is still 33 times lower
- If you set the weight factor torsion to 100, now the design might change to improve the torsional stiffness (as you rated it higher - meaning more important) in your weighted compliance result
Hope this helps. You can actually read the compliance from all loadcases in your *.out file of the optimization to see the compliance values in your load cases. I
Best Regards
Jan
0 -
Thanks for your answer, I think I understand how it works now! However, I am not sure if my model is correct, I receives the same result independent of the weight factors (which I understood could be the case) and also when I add one extra load case to the simulations. There is one warning in the .out file that I can't understand: 'SPC SID= 64 is referenced by SPCADD data but is not referenced by any bulk data.' Maybe that can affect the result?
Please find two .fem files attached, one model with two load cases and one model with three.0 -
Hellp Linn,
I just had a quick look at your model. There are large differences in the compliance / displacements of the models:
- The load case CICP shows almost no displacement --> meaning low compliance
- the load case RUC shows high displacement --> thus you have a high compliance (factor 100 compared to CICP).
In the optimization you set the weight factor of loadcase RUC to 100, which means that the compliance is now 100 x 100 --> 10.000 times higher than the compliance of load case CICP. Therefore your optimized design will be driven by loadcase RUC only and loadcase CICP has no effect on the structure. To change, set the weight factor CICP to 100 and the weight factor RUC to 1 and then you should see an effect.
Some more observations I made in your model:
Your model seems to be scaled in mm, but your material has a Youngs Modulus which seems to be scaled in N/m² (if I understand it correctly). Please make sure that the model size and material are both scaled in the same unit (either m or mm).
The warning message means, that you have summarized some areas with constraints (loadcollector with SPCADD Card). The loadcase CICP references a SPCADD Card with the Constraint IDs (Loadcollector IDs) 35 & 36 --> both can be found in your model, one on the top and one in the middle of the mandibula.
The load case RUC references the constraint IDs 36 & 64. However the set 64 is not present in your model. It might have been deleted by you earlier or it might have got lost. You might want to check the displacements in performing an analysis only and see if there are constraints missing.
Best Regards
Jan
0 -
Hi Jan,
There was one of the constraints in load case RUC that disappeared when I exported the .fem file, but I have solved that problem now and the results makes more sense now. When I only have weighting factor 1 for both of the load cases is the final result as if I only applied RUC, and if I increase the weighting factor for load case CICP a lot I can see a difference in the optimized design.
Thanks for the help, and thanks for reminding me about the units!0