mid surface meshing method
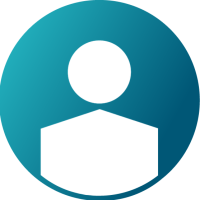

Answers
-
Hi Suresha,
One reason is to reduce to total number of DoFs compared with solid elements. Solid elements have 8 nodes and shell has only 4 (1st order elements).
Second reason is solid elements may not capture the geometry as good as shell elements specially in curvatures and fillets.
shell elements capture good bending behavior compared to solid elements. Solid elements will do capture but you need more number of layers of solid elements which means increased number of DoFs, time and disk space.
0 -
Altair Forum User said:
For what reason meshing is need to be done in mid surface only
Not 'only', but 'often'
/emoticons/default_smile.png' alt=':)' srcset='/emoticons/smile@2x.png 2x' width='20' height='20'>
In some cases, it's better to do simulation with internal or external surface of shell. In this case, for most FE solver, you have to take in account the excentricity of mesh comparing to mid-surface of shell structure.
0 -
Midsurface concept is used for most of the plastic parts (trims) and sheet metal parts. Extraction of miss ur face is done and 2d shell elements are used for midsurface meshing . Because of this method, user can assign the overall thickness (for the elements ) of the part which is assigned half to the upper side and half to the lower side. Shell elements also results in lesser computational cost as compared 3d meshing.
0