Pressing force for fitment analysis
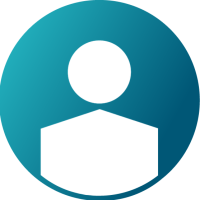

Hello All,
I'm doing fitment analysis of shaft and hub with an interference of 110 microns
and want to analyse
1.deformation in each component.
2.pressing force required for fitment.
3.Interference pressure.
can anyone tell me which control card should i use for the above output requests?
Regards,
Ganesh M
Answers
-
Hi Ganesh,
There are two options for interference fit. First you can simulate the physical press fit process in RADIOSS. Define contact between the two parts, constrain one part and apply an imposed displacement on the other part and simulation the physical press fit process.
Second option is to use /INTER/TYPE24 contact and set INACTI=-1 which will apply forces to remove initial intersection caused by the press fit. The one limitation with INACTI=-1 is that it applies the force all at once and for large initial penetrations the force can be too large. To reduce the force you can use the STFAC option on /INTER/TYPE24. In the attached model, STFAC=0.25 seems to give reasonable results. Run the model with STFAC=1 (default) see the difference. I ran the attached model in RADIOSS version 2017.1 but 14.0.230 or 2017.0 should also be fine. Please review the attached.
0 -
I have simulated the same, please have a look over it. but my objective is to get the value of frictional force required to press the shell into the hub. for that i need to introduce appropreate card. I am new to HW.
0 -
Hi Ganesh,
The animation looks fine. Create an output block for the rigid body, so to see the force you can plot the force on this RBODY in a particular direction using T01 file in HyperGraph.
0 -
How can I make it axisymmetric. can you help me with the constraints?
hub id is 33.50 mm
and inner ring of is 34.60
there is an interference of 110 microns.
want to simulate process and identify pressing force required and deformation in individual Component..
in actual case, we keep hub on table and outer ring on hub. then we press the outer ring by pressing plate.
in this case axial direction is Z. my loading condition is
X Y
0 0
0.1 23 mm in z (pressing plate displacement)
0.15 23 mm in z (pressing plate displacement)
0 -
Hi Ganesh,
Just let us know why you want to try with axisymmetric analysis as there are many restrictions on axisymmetric modeling for RADIOSS solver.
0 -
just to save time. Thats it.
0 -
Hi Ganesh,
For axisymmetric analysis there are many modelling restrictions and also all the normal results extracted are also not available for axisymmetric cases and so we normally don't recommend axisymmetric approach.
For saving time, you can try varying the imposed load curve, ie instead of ramping in 0.1 you can ramp the load in .03 or .05.
Also, you can introduce time step control (/DT/NODA/CST) so that you can save run time, but keep the mass error less than 5%.
0 -
okay, thanks George.
I have simulated the process. but my results are varying from actual. i thought there might be issue with the constraints.
i Kept hub restricted in axial direction and allowed disp to pressing plate in axial direction. do i need any other constraints addition to above.
0 -
Hi Ganesh,
Normally for axisymmetric we use 2D elements to model them. Use N2D3D = 1 for /ANALY card in the Starter file and ensure that the elements are defined in YZ plane and their normals have to be in the positive X-position.
Let us also know the contacts you have used in this model. Also please share the .h3d of this simulation or atleast the .gif of the simulation.
0