Sizing
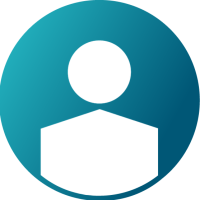

hello everyone,
i have a different result for the fe-analyse for my surface modell which i want to use for sizing to the results of the fe-analyse of the solid model.
the result of the sizing is incorrect too...
so first i need help to make the same fe-analyse results and second for the correct sizing setup.
both models are below.
thanks for your help and best regards.
Find more posts tagged with
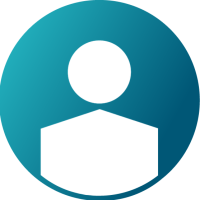

Hey, first of all thank you very much for your reply.
when the shell element size is small compared to thickness it loses validity. Solid elements are more appropriate for this object and you can perform shape optimization instead.
but i have a thickness defined in the property. and i can´t use solid elements because there are no solids..
Constraining the hole where loads are applied effectively eliminates this load. I suggest you perform inertia relief analysis (PARAM>INREL>-2) instead.
oh okay i never heard about that. the problem is that i have my deadline of the project soon and can´t deal with a whole new topic. what exactly is happening when i make (PARAM>INREL>-2)?
i have make both analyses with (PARAM>INREL>-2) and the resuts are unfortunaly very different
surface modell:
<?xml version="1.0" encoding="UTF-8"?>
solid modell:
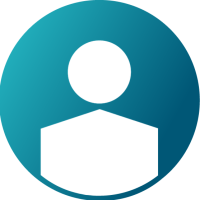
Glad to help.
Perhaps there is still misunderstanding: shell elements can not be used for this object. Use the edited model meshed with tetra solid elements (or hexa/penta mesh) with solid property assigned. Define shape pertubations using HyperMorph and perform shape optimization.
PARAM>INREL>-2 is inertia relief analysis. It makes possible simulation with no constraints, like satellite floating in space or aeroplane flying through the air. In your model it is best to use this option as the loads are applied to both holes at the same time. If you constrain the hole with load acting on that hole then this load will have no effect.
OptiStruct New Feature - Inertia Relief for LGDISP - Altair University
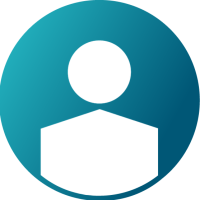

thanks again.
Perhaps there is still misunderstanding: shell elements can not be used for this object
yes i know that. shell elements are only for the surface modell. and the surface modell is needed for the sizing.
Define shape pertubations using HyperMorph and perform shape optimization.
but i have to do the size optimimization. or is it possible to optimize the thickness with the shape optimimization. i´ve never did that before...
PARAM>INREL>-2 is inertia relief analysis. It makes possible simulation with no constraints, like satellite floating in space or aeroplane flying through the air. In your model it is best to use this option as the loads are applied to both holes at the same time. If you constrain the hole with load acting on that hole then this load will have no effect.
what is the difference between -2 and -1 with support?
okay thank you very much. for the background: the modell is a swing of an industral robot. the loads are the peak from the turning process of 90°.
the result of the fem shows just 10 MPa under this load i think thats much to les...
| Kraft x [N] | Kraft y [N] | Kraft z [N] | M x [Nm] | M y [Nm] | M z [Nm] |
LO | -4545 | 100734 | -1351 | 82862 | -1788 | 26811 |
LU | 5191 | -85014 | 1806 | -82867 | 1772 | -26812 |
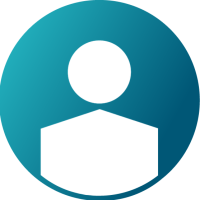
but i have to do the size optimimization. or is it possible to optimize the thickness with the shape optimimization. i´ve never did that before...
Size optimization defines ideal component parameters, such as material values, cross-section dimensions and thicknesses. Shape optimization is different from freeform (topology) optimization in that it is used once the component’s topology has already been defined. Topology optimization is used to generate material layout concepts whereas shape optimization refines and improves the topology within the concept.
In shape optimization, the outer boundary of the structure is modified to solve the optimization problem. Using finite element models, the shape is defined by the grid point locations. Hence, shape modifications change those locations.
Size optimization can not be done with solid elements. Thickness can be optimized using solid elements by first defining shape perturbations and the performing shape optimization. Refer to attached videos and documents for more details.
what is the difference between -2 and -1 with support?
-2: Requests inertia relief analysis without the need for a SUPORT/SUPORT1 entry (automatic)
-1: Requests that inertia relief be performed. SUPORT or SUPORT1 cards are required in the bulk data section to restrain rigid body motion.
the result of the fem shows just 10 MPa under this load i think thats much to les...
In the latest model you shared, each load is solved in separate loadsteps- maybe some of the loads are acting at the same time, which can cause higher stress. Have you done mesh convergence study?
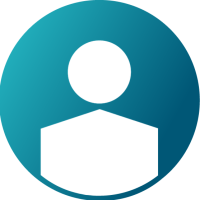

okay thanks for the information about shape optimization. but i would prefer the sizing because my prof said i should do that. is this possible to?
In the latest model you shared, each load is solved in separate loadsteps- maybe some of the loads are acting at the same time, which can cause higher stress. Have you done mesh convergence study?
no the loadsteps are time points while the robot is turning.
the model (name: reanalyse interpretation) before was only with the loads of time point five because that one is the most critical.
Have you done mesh convergence study?
what is this? sorry i´m ery new with the programm...
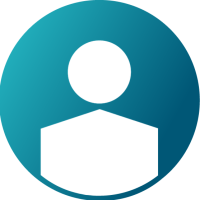
Again: shell elements can not be used to model this object, therefore size optimization can not be done. Modeling with solid elements and performing shape optimization will give optimized thickness dimension equivalent to optimized thickness of shell property in size optimization.
About mesh convergence:
https://enterfea.com/correct-mesh-size-quick-guide/
If you plan to do a convergence check, consider performing at least one refinement of the model after the first run. If neighboring elements display large differences in stress, the gradient was probably not captured in these areas, therefore some mesh refinement is recommended. In general, increasing the number of nodes improves the accuracy of the results. But at the same time, it increases the solution time and cost. Usual practice is to increase the number of elements and nodes in the areas of high stress (rather than reducing the global element size and remeshing the entire model) and continue until the difference between the two consecutive results is less than 5 to 10%.
I recommend you to go through free ebook Practical Aspects of Finite Element Simulation (A Study Guide) which covers 9.12 Mesh Density And Solution Convergence.
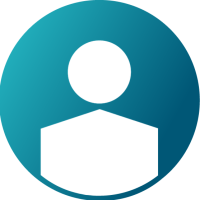

Again: shell elements can not be used to model this object, therefore size optimization can not be done.
Okay.. but why can't i Use the surface Modell with shells? You say because of h/l but i definded a thickness of the Shell... i wanted to do it like https://youtu.be/mfpDHfM4svQ
Thank you very much for your Help!
I will try to learn the shape optimization and the mesh convergence.
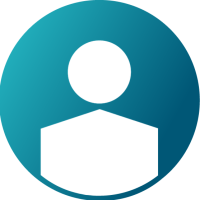
In the surface model the thickness of shell is h=30-50mm and average element length is l=10mm, which gives ratio h/l=3-5. Thin shells are valid only when ratio h/l does not exceed 0.1, but in your model this ratio is exceeded by 30-50 times! Please refer again to the first post why this is invalid.
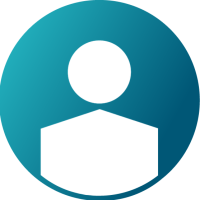

allright, now my slowly mind has understood, thanks a lot for your patience!
Hi,
when the shell element size is small compared to thickness it loses validity. Solid elements are more appropriate for this object and you can perform shape optimization instead.
<?xml version="1.0" encoding="UTF-8"?>
Quote
https://www.linkedin.com/pulse/shells-vs-solids-finite-element-analysis-quick-review-kuusisto-p-e-
Constraining the hole where loads are applied effectively eliminates this load. I suggest you perform inertia relief analysis (PARAM>INREL>-2) instead.
Unable to find an attachment - read this blog