Moving from FEA to MBD – Understanding the Key Differences and Fundamentals
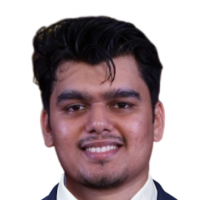

Check out MotionView/MotionSolve’s product webpage for info on more features, releases, and capabilities. You can download the latest version of MotionSolve in the Altair One Marketplace.
Learn more about Altair One and Community here.
Aspect | FEA (Finite Element Analysis) | MBD (Multibody Dynamics) |
---|---|---|
Primary Purpose | Structural analysis: stress, strain, deformation, fatigue, and thermal effects. | Motion analysis: forces, accelerations, kinematics, and system behavior over time. |
Body Representation | Uses meshed finite elements. | Uses rigid and flexible bodies with mass and inertia properties. |
Computational Demand | High (solves large systems of partial differential equations). | Lower (solves equations of motion for interconnected bodies). |
Physics Considered | Governs stress-strain behavior using material properties (elasticity, plasticity, etc.). | Solves equations of motion based on Newton-Euler dynamics. |
Primary Inputs | Material properties, boundary conditions, loads, and constraints. | Initial conditions, constraints, forces, torques, and motion drivers. |
Primary Outputs | Stress, strain, deformation, modal frequencies, fatigue life. | Displacements, velocities, accelerations, reaction forces, and joint loads. |
Typical Applications | Structural integrity, fatigue life, thermal stress. | Mechanism design, vehicle dynamics, robotics, aerospace mechanisms. |
Why MBD is a Better Choice for Certain Applications?
Solving Real-World Motion Problems
- Simulates joint movements, contact interactions, and force transmissions to ensure functionality before testing.
Faster and More Efficient Simulation
- Uses Newton-Euler or Lagrangian methods for quick, mesh-free iterations and optimization.
Understanding Kinematics and Dynamics
- Analyzes joint reactions, actuator loads, and system dynamics without complex boundary conditions.
Integration with Control Systems
- Supports co-simulation with motors, hydraulics, and electronics for robotics, automotive, and aerospace using Altair Twin Activate.
Optimizing Mechanism Design
- Improves linkages, gears, belts, and pulleys for efficiency and durability.
Critical for Automotive, Robotics, and Aerospace
- Used in various applications like suspension design, robotic motion control, and aerospace mechanisms to ensure performance.
Transitioning from FEA to MBD – Understanding the Fundamentals
For engineers experienced in Finite Element Analysis (FEA), moving to Multibody Dynamics (MBD) can seem like a significant shift. To make this transition smooth, engineers must develop an understanding of kinematics, kinetics, constraints, and system-level modeling. This section provides a step-by-step guide for transitioning from FEA to MBD, along with the basic physics principles that form the foundation of multibody simulations.
Rigid vs. Flexible Bodies
- In MBD, components are typically considered rigid bodies with mass and inertia properties. This simplifies calculations by assuming that deformations are negligible.
- However, MBD also supports flexible bodies using reduced-order techniques like modal flexibility (Craig-Bampton method), allowing engineers to incorporate deformation effects while maintaining computational efficiency.
- Transition Tip: Instead of meshing a component as in FEA, MBD requires defining its mass, center of gravity, moments of inertia, and connectivity to other bodies.
Degrees of Freedom (DOF) and Constraints
- In FEA, each node in a mesh has translational and rotational DOFs. In MBD, bodies have 6 DOFs (3 translational + 3 rotational) unless constrained by joints and forces.
- Constraints such as revolute, cylindrical, translational, spherical, and planar joints limit movement and define how bodies interact.
- Transition Tip: Instead of boundary conditions like fixed or pinned nodes in FEA, MBD uses kinematic joints and constraints to restrict motion realistically.
Load Applications in MBD
- In FEA, loads are applied as forces, pressure distributions, or thermal effects. In MBD, loads include:
- External forces (gravity, aerodynamic forces, user-defined inputs).
- Joint forces (torques, damping, stiffness).
- Contact forces (normal and frictional forces when bodies collide).
- Transition Tip: Unlike FEA, where force distribution leads to stress fields, MBD focuses on resultant reaction forces at joints and contacts.
Equations of Motion and Solvers
- In FEA, the system is typically solved using static or dynamic equilibrium equations involving large stiffness matrices.
- In MBD, simulations rely on Newton’s Laws and solve equations of motion over time using numerical solvers.
- Transition Tip: Instead of solving stress-strain relationships, MBD solves for positions, velocities, accelerations, and reaction forces using time integration.
Basic Physics Behind MBD
Newton’s Laws of Motion
MBD relies heavily on Newton’s Laws, which describe the relationship between motion and forces:
- First Law (Inertia): A body remains in uniform motion unless acted upon by an external force.
- Second Law (Force & Acceleration): F=ma, which forms the basis of MBD simulations.
- Third Law (Action-Reaction): Forces exerted by one body on another result in equal and opposite reactions.
These principles govern the way forces and constraints influence system behavior in MBD.
Kinematics vs. Kinetics
- Kinematics studies motion without considering forces (e.g., velocity and acceleration of a link in a mechanism).
- Kinetics studies motion with forces (e.g., the torque needed to rotate a robotic arm).
- MBD combines both to simulate real-world motion and force interactions.
Work and Energy Principles
- The work-energy theorem states that the total work done by forces on a system changes its kinetic energy.
- MBD accounts for potential energy (springs, gravity), kinetic energy (moving bodies), and dissipative forces (damping, friction).
Vibrations and System Stability
- Although MBD primarily deals with rigid body motion, flexible bodies in MBD can exhibit modal behavior like FEA.
- Engineers can analyze natural frequencies, damping effects, and resonance in mechanical systems using MBD.
Steps for FEA Users to Get Started with MBD
- Start with Simple Rigid-Body Simulations
- Build a basic two-link mechanism with revolute joints and observe its motion.
- Apply forces and torques to understand their effects.
- Learn Constraint Handling and Joint Types
- Practice using revolute, prismatic, spherical, and planar joints to understand mobility restrictions.
- Understand Forces and Contact Mechanics
- Use MBD to model gear interactions, cam-followers, and belt-pulley systems.
- Explore Flexible Body Dynamics
- Convert an FEA-derived flexible component into an MBD modal reduced-order model (ROM) and analyze how it affects system motion.
- Integrate with Control Systems
- If working with mechatronic systems, explore co-simulation with control algorithms using MATLAB/Simulink or Altair Activate.
Learning Resources
For a robust understanding of MotionView/MotionSolve, the most effective approach is to explore the comprehensive courses available on the Altair Learning website. These in-depth eLearning modules not only provide theoretical knowledge but also offer practical examples and exercises, enabling you to develop proficiency in utilizing the software.
MotionView/MotionSolve Introduction v2023 eLearning