Improving Prosthetic Knee Performance using Inspire Motion
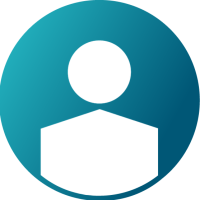

INTRODUCTION
Prosthetic knees have seen significant improvements over the last several decades. Originally, single axis prosthetic knees helped amputees to walk again. However, they lacked the stability and range of motion of real knees while requiring an unnatural gait. The polycentric knee was developed to address these concerns at the cost of a more complex (and heavy) mechanism. Now use of lightweight materials like plastic, aluminum, carbon fiber, and titanium make polycentric prosthetics very practical and useful.
Today, motors and pneumatic or hydraulic actuators are being implemented to provide extra support during more difficult activities like climbing a hill or walking up stairs. Microprocessor-controlled knees can even collect data on a user’s gait and provide extra support to make walking with a prosthetic feel easy and natural.
Multibody dynamics (MBD) is one powerful tool for aiding in the development of prosthetic knees. As microprocessor-controlled knees are developed, control algorithms must be developed to create natural gaits which improve user stability. MBD provides the ability to create a virtual model of the prosthetic. The model can be used to test different control algorithms in order to validate performance. By testing and improving algorithms in a virtual environment, the conditions of walking can be emulated without posing risk to the user’s testing the algorithms.
Lightweight prosthetics are a second area of development critical to improvement of modern prosthetic knees. Lightweight prosthetics make actions like walking and running easier, improving the quality of life for prosthetic users. Altair’s Inspire is particularly well-suited to aid in the lightweighting of prosthetics. Multibody dynamics simulation can emulate the conditions of walking or running. In the same environment, loads can be extracted and used to optimize prosthetic knee geometry. Performance can be validated using powerful FEA tools. Finally, 3D printing tools built into Inspire allow the parts to be sliced and printed with optimal supports.
Lightweighting a Prosthetic Knee MBD ModelInspire makes the setup of MBD models and implementation of optimization quick and easy.
MBD Model Setup
- Geometry can be imported or created in Inspire.
- The calf is grounded or fixed.
- Rigid groups are created for parts with no relative motion.
- The joint tool automatically detects and creates all the joints.
- The Joint Tool Automatically Detects & Creates Joints
- An actuator is created to define the knee’s motion and loads.
- A motion analysis can be run to check the motion of the model.
MBD Prosthetic Knee Flexure
Optimization
- Each part which is to be optimized is turned into a design space.
- The components are partitioned at the joints.
- Draw direction controls can be employed to create parts which can be manufactured in a number of ways including:
- Milling
- Extruding
- Stamping
- Casting
- 3D Printing
- Shape controls can be used to force the optimized shape to be symmetric across a plane or radially.
Link Prepared for Optimization – 49 grams
- After preparing the part, the part can be optimized to minimize deflection or minimize mass.
Optimized Part – 27 grams
- The optimized part can be fitted with PolyNURBS to smooth the part and eliminate sharp corners
Optimized & Smoothed Part
SOFTWARE REQUIREMENTSInspire (2024 or newer)
MODEL FILES RUNNING THE MODEL- Open a session of Inspire.
- Open Prosthetic_Knee_Baseline.stmod or Prosthetic_Knee_Optimized.stmod in Inspire.
- Run a motion analysis to view the prosthetic’s motion.
- Run analyze part to view the stresses on a component.
Through optimization the total mass of the assembly decreased from 540 grams to 433 grams, a reduction in mass of nearly 20%. In the load cases used for optimization the leg supports 25 kg of mass. Stresses increased from a peak of 105 MPa to 159 MPa. The stresses are well below the 760 MPa yield strength of the titanium components. In addition to predicting stresses, Inspire includes a force explorer for visualization of the forces and torques acting at joints, contacts, and fasteners.
Baseline – 540 grams
Optimized– 433 g grams
Baseline – 540 grams
Optimized – 433 g grams
Baseline Knee Stresses (Left) | Optimized Knee Stresses (Right)
The stress comparison between the baseline and optimized links uses the boundary conditions or loads developed during rigid body motion. This tends to overpredict stress but serves as a useful and quick tool for comparison. Applying flexible bodies accounts for the deformation of the bodies during motion and predicts more accurate stresses.
Visualization of the Forces Between Bodies using the Force Explorer
Stresses during Motion with Flexible Bodies
CONCLUSIONProsthetic knees have come a long way from the initial single axis knees. Advanced microprocessor-controlled polycentric knees making use of tiny motors and actuators make walking and running easy and natural for amputees. Key to the development of modern prosthetics is simulation. Multibody dynamics, finite element analysis, and optimization lead to lighter, stronger prosthetics while providing a testbed for control algorithms seeking to improve the lives of amputees. In addition to the simple knee flexure demonstrated with this model, complex motions and load cases are possible like walking, running, and squatting. By leveraging powerful simulation tools, prosthetics can be designed to be better than ever before.
AUTHORSJohn Dagg, Systems Engineering Intern
Christopher Fadanelli, Solution Engineer - Systems Integration
Ananth Kamath Kota, Global Technical Manager - Systems Integration