Flow Drilling Screw simulation with SPH
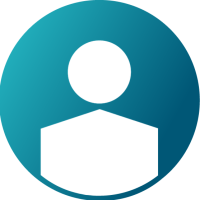
Hello,
I'm trying to simulate the Flow Drilling Screw process using Radioss. If needed, details about this process can be easily found on the Internet.
I modelled two overlying aluminium plates with SPH, then a solid mesh screw subjected to a longitudinal force and a rotational speed is supposed to penetrate the plates by extruding the SPH particles up and down (for this reason I did not add a failure that would have deleted the particles, instead).
The main problem with the simulation is that, after roughly one third of the screw correctly penetrates the plates, the simulation stops due to total mass error limit reached. The error appears in the only line where the timestep is determined by the interface between screw and plates. The interface is of type 7 with the recomended parameters excluding Istf=1000 that should be appropriate for SPH.
Does anyone know what can be the cause of the problem?
I'm attaching the .out file.
Regards
Answers
-
Hi
Please try to define Stfac=0.1 and the Gap_min as the 1/2pitch of the sph cell distribution, as Gap_min for /INTER/TYPe7 cannot be 0.0
please refer to the documentation for more details
I Hope this is helpful
Regards
0 -
Thanks for your reply,
I had actually solved the problem by setting Stfac=0.5 and Gap_min as 1/6 of the SPH cell distribution pitch. Now the model seems to work properly. Anyway, you confirmed that my approach was right.
Thank you again,
Best regards
0