CFD-DEM model validation
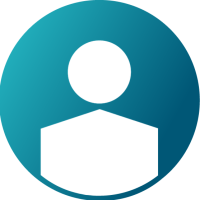

Hi experts,
I’m doing an Acusolve-EDEM bidirectional coupling simulation, but the simulation result is different from the phenomenon observed in experiment. Both results are shown below:
It is noticed that the cavity size in simulation is quite smaller than that in experiment. By the way, the contact parameters in DEM have been calibrated.
I tried to do mesh sensitivity study. According to EDEM - Coupling with Altair CFD, minimum acceptable mesh volume is 0.1*particle volume. The particles are spherical and have a uniform diameter of 4.5 mm (volume is 47.7 mm^3), so I set the mesh size to 3.5 mm and the mesh type is tetrahedral (estimated volume is 5.05 mm^3). However, the new result is only slight different from previous one with coarse mesh, as shown below:
Currently I think there are three options for the next step, but I’m not sure whether these choices are proper or not:
- Refine the mesh (global or local)
- Reduce the CFD timestep size (5e-5 s / 2e-5 s)
- Change drag model
I will be grateful if there’s some advice on how to do next. The simulation files is attached.
Regards,
Gary
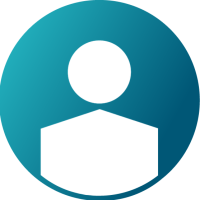

I suggest using the CFD mesh size about 0.8 mm. This gives you 5-6 elements per EDEM particle. Or maybe at least 1.0 mm to get maybe 4 elements per particle.
I would also use a Zone refinement/control to get similar size on the walls near the pipe. Right now there's a very large size jump to the large mesh on the outer walls near the pipe. Also extend that similar size to get better resolution of that inlet 'jet' farther into the domain. The current mesh gets coarse very quickly so the jet is washed out. (This may be the larger reason for the void not extending farther into the domain - the jet is not extending into the domain.)
It's normally better to include some length of pipe/duct and have the inlet going into that pipe, rather than into the larger volume itself. But maybe try those other items first.
Hi Acupro,
Thanks for your advice. However, I tried mesh refinement and a longer pipe, and they don't work. Are there any further suggestions?
The latest model is attached.
Regards,
Gary
Hi Acupro,
Thanks for your advice. However, I tried mesh refinement and a longer pipe, and they don't work. Are there any further suggestions?
The latest model is attached.
Regards,
Gary
That still has the CFD mesh fairly coarse away from the pipe. I would suggest using 1.0 or 1.5 mm fluid mesh elements throughout the entire volume that has the EDEM particles. All the particles above need to move if there's going to be no particles near the end of the inlet tube.
Probably increase maximum stagger iterations to 4 also, to allow for better convergence of the equations each time step.
That still has the CFD mesh fairly coarse away from the pipe. I would suggest using 1.0 or 1.5 mm fluid mesh elements throughout the entire volume that has the EDEM particles. All the particles above need to move if there's going to be no particles near the end of the inlet tube.
Probably increase maximum stagger iterations to 4 also, to allow for better convergence of the equations each time step.
Of course, you'll also want to make sure your EDEM particles are defined properly - density, and other settings/properties.
I suggest using the CFD mesh size about 0.8 mm. This gives you 5-6 elements per EDEM particle. Or maybe at least 1.0 mm to get maybe 4 elements per particle.
I would also use a Zone refinement/control to get similar size on the walls near the pipe. Right now there's a very large size jump to the large mesh on the outer walls near the pipe. Also extend that similar size to get better resolution of that inlet 'jet' farther into the domain. The current mesh gets coarse very quickly so the jet is washed out. (This may be the larger reason for the void not extending farther into the domain - the jet is not extending into the domain.)
It's normally better to include some length of pipe/duct and have the inlet going into that pipe, rather than into the larger volume itself. But maybe try those other items first.
I suggest using the CFD mesh size about 0.8 mm. This gives you 5-6 elements per EDEM particle. Or maybe at least 1.0 mm to get maybe 4 elements per particle.
I would also use a Zone refinement/control to get similar size on the walls near the pipe. Right now there's a very large size jump to the large mesh on the outer walls near the pipe. Also extend that similar size to get better resolution of that inlet 'jet' farther into the domain. The current mesh gets coarse very quickly so the jet is washed out. (This may be the larger reason for the void not extending farther into the domain - the jet is not extending into the domain.)
It's normally better to include some length of pipe/duct and have the inlet going into that pipe, rather than into the larger volume itself. But maybe try those other items first.