Boundary layer parameters requirement in quasi-2D CFD-DEM problem
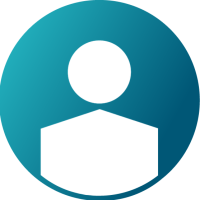

Updated by Gary_Ko_460
Hi Support,
I’m doing a CFD-DEM problem with Acusolve and EDEM. The geometry is a thin slot (width/thickness/height: 60/2/150 cm), and the side walls are in non-slip condition. The other boundary conditions and particle positions are shown below:
The particle diameter is 4.5 mm, which means the geometry can accommodate approximately 4 particles in the thickness direction, so I’d like to have 4 layers of elements in the thickness direction (average mesh size: 5 mm).
My questions are as follows:
- Because of the non-slip wall condition and also because there are only 4 layers of elements in the thickness direction, I guess that I should add boundary layer mesh to avoid low flow velocities near walls. Is that correct?
- Assuming that I need boundary layer mesh, however, the flow field in the boundary layer is not my focus. Do I need to carefully calculate the boundary layer parameters, such as first layer thickness and growth rate?
I would be grateful if you could help me in this matter.
Regards,
Gary