Large deformation in rubber sample
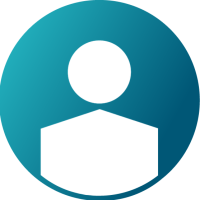
I am trying to model a rubber material that has 300%+ elongation capacity. I don't need to model the rupture mode, just the fact that it can deform elastically and return to its original shape. I tried with LAW2 and LAW42 but my solid elements (BRICK) just seem to explode when I reach close to 100% elongation. I tried different ISOLID (1,14,24), but I always get the same result.
Any advices welcome, thanks. Images of model and .rad, .out below.
<?xml version="1.0" encoding="UTF-8"?>
<?xml version="1.0" encoding="UTF-8"?>
Answers
-
0
-
Hi,
Using LAW42 would be recommended since it is a rubber material.
Using Ismstr = 10 is recommended with hyperelastic material laws. As HyperMan shows, /PROP/SOLID, Isolid=14 with Ismstr = 10 works.
Or you can use /PROP/SOLID, IHKT = 2 with Isolid = 24 (HEPH) and Ismstr = 10 which runs a little faster and also works.
We have this statement in the comments of /PROP/SOLID but I realize it is easy to miss.
For foam or rubber materials such as laws 38, 42, 69, 82 and 88, it is recommended to use IHKT = 2 with Isolid = 24 (HEPH) and Ismstr = 10, 12 (Lagrange type total strain).
Thanks,
Andy
0 -
Thanks Hyperman and Andy for the edited model and the pointers to changing the PROP parameters. I had missed the comments.
Thank you for your help.
0