Doubt about boundary condition and material
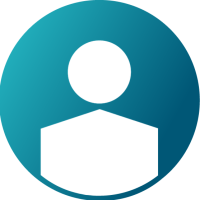
Hi,
I am running a cfd simulation of oil lines to determine pressure drops with HyperWorks CFD 2021.1. Having a non-planar fluid inlet surface (fluid enters along a cylindrical surface, there is a valve from which oil enters along the entire inner side area of this cylinder) how do I enter the boundary condition that has a volumetric (or mass) flow rate? I filled the hole and used the volumetric flow entering on the outer surface of the filled hole (i.e., the fluid enters the domain from the circular surface as if from a pipe), is this correct? Is there another solution?
I have another doubt about units, is the viscosity when I create a material the dynamic viscosity (in Pas=kg/ms) or the kinematic viscosity (m^2/s)? (I used for the other input data: distance in m, density in kg/m^3, specific heat in J/kgK and conductivity in W/mK).
I also have the problem of inflow at the outflow boundary, is it correct to extend the volume to have the outlet farther away (to allow the flow to fully develop) and have a reduction in area in the last part of the extended volume to accelerate the flow? Is there any other solution?
I have also the problem of outflow at the inflow boundary, and the value remain constant for the whole simulation, how can I solve also this problem?
Thank you very much in advance
Best Answer
-
Fededea said:
Ok, thank you very much!!
So just to be sure: I fill the cylindrical hole and then I extrude the opposite face of this new volume outside the original volume? And then I put the volumetric or mass flow rate as inlet?
I have also extended the domain over the outlet to not have the inflow at outflow warning, is it correct to put to these domain’s walls the slip condition? Or will be ok also with the no slip condition?
Thanks in advance!!
Yes - something like the image below. The inlet is 'extruded' away from the original cylindrical face, and a little bit on the opposite side as well (just so you don't have the incoming flow hit the back wall immediately where it needs to turn to go into the rest of the domain. It likely won't give the same inlet profile as with a constant around the cylinder - but it will at least get the flow entering.
With the outlet extension away from the action/turning in the flow, either slip or wall should be fine. Slip will contribute less to the overall pressure drop.
0
Answers
-
You should be able to use the mass-flux (really mass flow rate) inlet, even on a cylindrical inlet. Have you tried that?
Is this a single inlet - single outlet case? Or do you have multiple inlets/outlets? Could you attach some images - especially for the region at/near the inlet?
Could you attach the representative .inp file also?
The viscosity for material properties is the absolute/dynamic viscosity - in kg/m-s.
1 -
acupro_21778 said:
You should be able to use the mass-flux (really mass flow rate) inlet, even on a cylindrical inlet. Have you tried that?
Is this a single inlet - single outlet case? Or do you have multiple inlets/outlets? Could you attach some images - especially for the region at/near the inlet?
Could you attach the representative .inp file also?
The viscosity for material properties is the absolute/dynamic viscosity - in kg/m-s.
Yes I have tried, but if i select the whole cylindrical surface I get the error non-planar inlet and if i select one surface and i set the boundary with the half of the flow rate and the half to the other one in the log I have the warning outflow at inflow boundary.
There is one inlet and one outlet, I attach some images at this answer. One with the model with outlet and inlet, and one with a detail of the inlet (the oil enter with a constant flow the domain from the selected surfaces (yellow in figure) on the whole surface from a valve). Could be that I need to use constant inlet with the average flow velocity (flow rate/surface=average velocity)?
Thanks for the answer!!
EDIT: I add the .inp file
0 -
The non-planar inlet is allowed in version 2022.3. See the updates page:
https://help.altair.com/hwcfdsolvers/acusolve/topics/chapter_heads/whats_new_r.htm#whats_new_r
Inflow on Arbitrarily Surface
Mass flow inlet conditions are no longer limited to planar surfaces. Cylindrically curved or arbitrarily shaped surfaces can now be used to define inlet mass flow conditions. The flow direction is relative to the local surface normal allowing for inlets on circumferential surfaces.0 -
acupro_21778 said:
The non-planar inlet is allowed in version 2022.3. See the updates page:
https://help.altair.com/hwcfdsolvers/acusolve/topics/chapter_heads/whats_new_r.htm#whats_new_r
Inflow on Arbitrarily Surface
Mass flow inlet conditions are no longer limited to planar surfaces. Cylindrically curved or arbitrarily shaped surfaces can now be used to define inlet mass flow conditions. The flow direction is relative to the local surface normal allowing for inlets on circumferential surfaces.ok thanks, there are some solution instead for the 2021.1 version? Because in my computer there is installed this version and I can't install any update by myself.
0 -
Fededea said:
ok thanks, there are some solution instead for the 2021.1 version? Because in my computer there is installed this version and I can't install any update by myself.
I would suggest to try adding a tube/pipe so you can have a planar inlet - that leads to that cylindrical surface. Remove that cylindrical surface so it's just an opening to the rest of the domain. Maybe extend the pipe beyond the cylinder to the side opposite the new inlet as well.
0 -
Ok, thank you very much!!
So just to be sure: I fill the cylindrical hole and then I extrude the opposite face of this new volume outside the original volume? And then I put the volumetric or mass flow rate as inlet?
I have also extended the domain over the outlet to not have the inflow at outflow warning, is it correct to put to these domain’s walls the slip condition? Or will be ok also with the no slip condition?
Thanks in advance!!
0 -
Fededea said:
Ok, thank you very much!!
So just to be sure: I fill the cylindrical hole and then I extrude the opposite face of this new volume outside the original volume? And then I put the volumetric or mass flow rate as inlet?
I have also extended the domain over the outlet to not have the inflow at outflow warning, is it correct to put to these domain’s walls the slip condition? Or will be ok also with the no slip condition?
Thanks in advance!!
Yes - something like the image below. The inlet is 'extruded' away from the original cylindrical face, and a little bit on the opposite side as well (just so you don't have the incoming flow hit the back wall immediately where it needs to turn to go into the rest of the domain. It likely won't give the same inlet profile as with a constant around the cylinder - but it will at least get the flow entering.
With the outlet extension away from the action/turning in the flow, either slip or wall should be fine. Slip will contribute less to the overall pressure drop.
0 -
acupro_21778 said:
Yes - something like the image below. The inlet is 'extruded' away from the original cylindrical face, and a little bit on the opposite side as well (just so you don't have the incoming flow hit the back wall immediately where it needs to turn to go into the rest of the domain. It likely won't give the same inlet profile as with a constant around the cylinder - but it will at least get the flow entering.
With the outlet extension away from the action/turning in the flow, either slip or wall should be fine. Slip will contribute less to the overall pressure drop.
Thank you very much for all the clarification!
0