Modeling Fastener Failure in OptiStruct using Cohesive Material
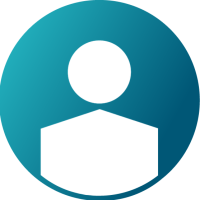
There are several ways to model fastener failure in Radioss explicit analysis. Elements can be deleted on the fly by manipulating conventional and connector-specific material models (for shell and solid elements) or force-deflection curves (for spring elements).
Some applications include discrete fasteners, adhesives and crack propagation (if a crack location is assumed).
Modeling failure in OptiStruct implicit analysis has not been so easy. Stress-strain or force-deflection curves with negative slopes or zero values cause convergence problems. Elements could only be deleted by stopping and re-starting an analysis with a model change.
In v 2020, OptiStruct has implemented cohesive materials and a solid element property that make it possible to delete elements from the model during an analysis as they fail. One of the new cohesive materials will be outlined along with the supporting property and damage models. The models will be compared, one solved in Radioss and one solved with the new OptiStruct cohesive capabilities.