Stress Analysis of Lattice Structures
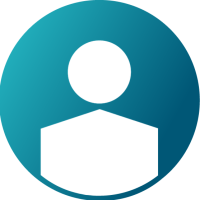

Abstract
The goal of this study was to perform stress analyses of lattice structures using two approaches, namely the traditional finite element method and the method of external finite element approximations, to demonstrate the viability of the two approaches.
Introduction
There are two broad approaches to modeling lattice structures for structural analysis. One is the direct approach in which the geometric details are modeled explicitly, and the other is an indirect approach in which the geometric details are not modeled explicitly but they are accounted for implicitly using an equivalent model. The focus of this study is the direct approach, which can be further classified into traditional finite element method and method of external finite element approximations.
Traditional finite element method: A detailed mesh is used to discretize the complex geometry of the lattice structure. For example, the microstructures of a lattice like the individual unit cells are modeled in detail. The elements used for the discretization are limited to certain shapes like trias, quads, tetras, pentas, bricks etc. The interpolation of the field of interest is also limited to simple polynomials. The effort required to create a good quality mesh, especially for a complex, random lattice structure is high. The memory and disk space requirements are also high due to the large size of the finite element model. The accuracy is governed by the quality of the mesh to a large extent. Though this is a viable and well-established approach for many industry applications, this may not be practical for stress analysis of complex lattice structures. Altair OptiStruct employs the traditional finite element method.
Method of external finite element approximations: In this approach also, the microstructures of a lattice like the individual unit cells are captured in detail. Structural analysis is performed using fully featured, not simplified, solid geometry without a mesh. This can be considered as a generalization of the finite element method in the sense that the finite elements used can be arbitrary geometrical shapes and the interpolation functions that approximate the field of interest can also be of an arbitrary class. Since this approach does not require a mesh, the effort required to perform structural analysis of complex lattice structures is much less compared to the traditional finite element method. Altair SimSolid uses a method for external finite element approximations that is fast, efficient, and accurate. The solution accuracy is controlled using automatic multi-pass adaptive analysis.
Lattice Geometries, Loading and Boundary Conditions
For this study, structural analyses of two unit-cell lattice structures, namely “Small Lattice” and “Large Lattice” of different complexity as shown in Figure 1, were performed using Altair SimSolid and Altair OptiStruct. The loading, which is an enforced displacement as shown in Figure 1, may appear to be a trivial case. However, this loading was chosen as this causes stress concentration in all the cells and hence was expected to pose a challenge for the solution convergence, especially with the automatic adaptivity in SimSolid. The dimensions of the models, units, magnitude of the loading and modulus values used are not critical as all the analyses performed were linear.
The stress labels of the SimSolid contour plots may show the units as there is no option currently to remove them. “Geom” in the labels in subsequent pages denotes the geometry import setting in SimSolid for the geometry input resolution. This dictates the number of facets used in storing the geometry internally in a faceted form. “Sol” in the labels in subsequent pages denotes the solution setting in SimSolid for the solution refinement level. The geometry import settings and the solution settings for the SimSolid runs were not exactly the same for both lattice geometries. As the complexity of the lattice geometry increases, higher resolution options for geometry and solution settings may be required and hence they were not the same for both cases. All the SimSolid runs were performed using version 2021.1.1 and all the OptiStruct runs were performed using version 2020.1. The result presented in this document for both SimSolid and OptiStruct is the von Mises stress. Displacement results are not presented as the primary focus of this study was to compare the stresses.