Quasi static analysis using Altair Radioss
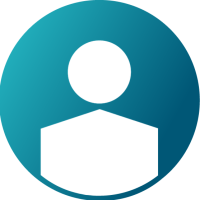

A three-point bending flexural test is a standard test in which a specimen is loaded under uniaxial bending stress. The test is performed to obtain material properties such as elastic modulus in bending, stress-strain behavior, and failure limits.
Some standards are used for this test. For example, ASTM D790 or ISO 178 are used for plastics; ASTM C1684 or C1161 are used for ceramics. In this article, we are going to follow the standard ISO 178.
As it is a trivial test, you may think that three-point bending tests are easy to simulate, but it is full of challenges for implicit analysis. Simulating using Altair Radioss, an explicit solver, might be faster in such cases.
The Standard ISO 178
The standard specifies the test conditions for three-point bending flexural test of plastics.
Dimensions | 80 mm x 10 mm x 4 mm |
Test speed | 2 mm/min |
Applicator radius | 5 mm |
Supports radius | 5 mm |
Distance between supports | 64 mm |
Quasi-static Problem
On this test, the specimen is just supported by the two cylinders and can translate and rotate in all six degrees of freedom, depending only on the contact and friction. So, from a static analysis perspective, the model is extremely unstable.
Altair Radioss is an explicit solver, meaning there is no need to search for a single absolute solution from the governing equations, satisfying all the convergence criteria. It directly computes the nodal acceleration and solves the dynamic equation. On the other hand, it is not unconditionally stable, thus, smaller time steps are required. In general, explicit codes are used for high strain rates and non-linear short-term problems. So, the question is, as the three-point bending test is a very long phenomenon, how can we simulate it using an explicit code?
Step 1 – Make the phenomenon time as short as possible
First, let’s run the starter file (_0000.rad) to check the natural time step of our model.
Considering a scale factor of 0.67 on the time step control, the natural time step of the model is around 5E-7.
Accordingly to the standard, the test speed is 2 mm/min, so, for a 5 mm push the process will take 150 seconds.
As expected, it is impossible to use this run time. Let’s consider a reasonable value of 200 thousand cycles.
For a run time of 0.1 seconds, around 200 thousand cycles are expected. The results look good as following.
Now we may ask, this simulation can be called quasi-static or not?
To answer this question, we need to check the kinetic energy and the Force x Displacement curve. In the case of a quasi-static event, the loading rate should be kept sufficiently low so that inertia forces are negligible, and the kinetic energy should remain zero or very small during the simulation.
Analyzing the graph, we can conclude that the simulation is quasi-static, as the kinetic energy remains zero throughout the simulation, and no noise is observed in the force x displacement curve.
Now, let’s try to optimize the model by reducing the run time to 0.01 seconds.
The stress results look the same, but the Kinetic energy has increased, and the Force x Displacement curve has a lot of noise. These aspects show that the time was too short to consider this a quasi-static simulation.
2.Use a Smooth Function
As you may know, the most turbulent phase of a displacement is the start and stop. In Radioss, we have a feature called Smooth function that slowly starts to apply the Displacement or Load, and slowly stops. With this curve, we can suppress the kinetic energy and reduce the noise on the Force x Displacement curve.
An improvement can be seen in both graphs, with a decrease in the kinetic energy and a reduction of the noise on the Force x Displacement curve.
Step 3 – Use dynamic relaxation with adaptive damping
Applying dynamic relaxation is an important step to get a proper quasi-static simulation using Altair Radioss. Although it is difficult to guess how much attenuation should be done, Radioss /ADYREL has almost no effect on the overall deformation of the object, but it is effective for fine vibrations. The period to be damped is automatically calculated and varies during the simulation.
To apply this change, all you have to do is add /ADYREL into the engine file. Results with /ADYREL:
Step 4 – Optimize the simulation time with Advanced Mass Scaling
Advanced Mass Scaling (AMS) is a feature that can significantly reduce the computation time of explicit simulations. This is similar to traditional mass scaling, except that the added mass does not increase the translation kinetic energy of the system. Thus, AMS can increase the time step without changing the physical mass of the model.
One should add the keyword “/AMS” to the starter file to apply AMS to a model, specifying which parts AMS will be used. AMS will be applied to the entire model if no parts are selected. The next step is to add the keyword “/DT/AMS” to the engine file, which will set the target time step and scale factor for AMS.
Method | Time step | Computational time |
/DT/NODA/CST | 5e-07 | 1 minute and 32 seconds |
/DT/AMS | 7e-06 | 17 seconds |
Advanced Mass Scaling shows a significant improvement in computational time with very close stress and strain results.
Note: Currently, there is a limitation using AMS with Smooth Function. For the fourth step, a standard function with a smooth shape was used. Our team is constantly working on enhancements, and this should be supported soon.
Summary
- Shorten the duration of the phenomenon.
- /FUNCT_SMOOTH for a smooth movement.
- Apply dynamic relaxation with /ADYREL.
- Improve the computational time with AMS.
On your next quasi-static simulation, try Altair Radioss.
The model can be downloaded here: Quasi Static Analysis
This article was originally made by Nobuyuki Fukuoka in Japanese. It can be found here