Modeling a uniaxial compression test in EDEM
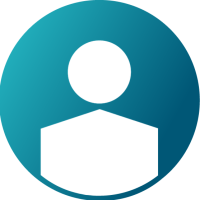

1 Introduction
The Uniaxial Compression Test (UCT) is used for the determination of the compressibility and Unconfined Yield Strength (UYS) of bulk solids in the pharmaceutical, cosmetics and consumer products industries among others [1,2]. The test can be used to determine the UYS more rapidly and at higher consolidating stress magnitudes than the more commonly used shear cell test. However, the measurements are performed on a non-critically consolidated sample which makes them relevant only in cases where the material is subjected to consolidation under confinement such as die compression processes [2].
The test consists of a consolidation stage where a bulk solid sample, confined in a rigid cylindrical vessel, is consolidated under a pre-defined uniaxial compressive stress using a piston. The confining vessel is then removed, and the sample indirectly sheared to failure by uniaxial compression in the unconfined state. The test procedure is summarized in Figure 1 and the resulting axial stress-strain curves are shown in Figure 2.
An EDEM model of the UCT test along with an EDEMpy post-processing script for the determination of the axial stress-strain curves is available in the EDEM calibration kits.
|
|
Figure 1: UCT test procedure (a) simulation setup, (b) sleeve filling, (c) levelling, (d) piston’s approach to test sample, (e) confined compression/ consolidation, (f) controlled unloading of test sample, (g) removal of sleeve after compression, and (h) unconfined compression
|
|
(a) (b) | |||
---|---|---|---|
Figure 2: Stress-strain response of the bulk specimen during UCT for (a) consolidation, and (b) unconfined compression.
|
|
2 Modeling methodology
The geometric elements required for the EDEM model are summarized in Figure 1(a) and include the base, sleeve, funnel, piston and a particle factory geometry. These can be modeled as frictional rigid bodies in EDEM with the exception of the factory which is modeled as a virtual geometry and the sleeve which is modeled as frictionless for simplicity. It should be noted that the frictional traction at the bulk solid – sleeve interface reduces the effective consolidation stress applied to the sample and the sleeve should be modeled as frictional if the stress reduction is expected to be significant. This may be the case when modelling highly frictional solids or solids that exhibit high lateral pressure ratios [3].
A meso-scopic modeling approach, whereby the bulk solid is modelled using numerical particles of an intermediate scale between the physical particle scale and the scale of the UCT test, is adopted in the interest of computational efficiency [4]. The meso-scale particles do not represent physical particles but a volume of powder and therefore reproducing the physical particle morphology and particle size distribution in the model is not meaningful [5]. Instead, two-sphere particles with an aspect ratio greater than 1.25 and a normal size distribution with a Coefficient of Variance of at least 15% are used to avoid artificial crystallization in the particle assembly [4]. The Edinburgh Elasto-Plastic Adhesive (EEPA) model is used to describe the particle contact mechanics. This model can capture the stress-history-dependent cohesive behavior of fine particulate solids, which are commonly characterized using a UCT test [4].
The test procedure is summarized in Figure 1. A funnel serves to guide the particles into the sleeve during filling and is subsequently used for levelling the sample surface, as illustrated in Figure 1(b) and Figure 1(c). The piston then approaches the sample as shown in Fig.1(d). The motion of the funnel and piston until this point are controlled using an linear translation kinematic. A uniaxial compression force is then applied to the piston using a force controller with a speed cap. After static conditions are obtained, the sample is unloaded by retracting the piston at a constant rate. The motion control settings for the piston are summarized in Figure 3. The piston retraction marks the completion of the confined compression stage of the test.
In the subsequent unconfined compression stage, the sleeve is lifted, and the sample is crushed to failure by the piston in the unconfined state, as illustrated in Figure 1(g) and Figure 1(h). The piston moves at a constant velocity controlled by a linear translation kinematic in this stage.
|
|
---|---|
Figure 3: Use of EDEM’s motion and force controllers for governing piston kinematics during (a) initial approach, (b) confined compression, and (c) unloading
|
|
The axial-stress strain response at various stages of the test is shown in Figure 4 and demonstrates the elastic ‘recoverable’ (ε_E) and a plastic ‘non-recoverable’ (ε_P) deformation of the sample. The UYS marked corresponds to the peak axial stress in the unconfined compression stage.
|
|
---|---|
Figure 4: State of stress and strain in the bulk specimen during the uniaxial compression test
|
|
Uniaxial compression tests produce measurements in the quasi-static flow regime where the macro-mechanical behavior of granular materials is strain rate independent. Therefore, the compression rate in the EDEM deck can be accelerated in the interest of computational efficiency as long as quasi-static flow regime conditions are maintained. A practical approach is to increase the strain rate while maintaining the inertial number defined in Equation 1 smaller than 1e-3 [6].
|
| ||
---|---|---|---|
3 Post processing with EDEMpy
The results from the uniaxial compression test can be automatically exported from the completed EDEM simulation deck using the Python script provided in the EDEM calibration kits. The script utilizes the EDEMpy library of functions for post-processing EDEM simulation data to compute and export the results in graphs such as the one shown in Figure 2 and comma-delimited files such as the one shown in Figure 5. The Python script file is accompanied by the settings file shown in Figure 6 which defines the key time steps and settings for post-processing the completed EDEM deck.
|
|
Figure 5: Extracted responses from the EDEM simulation deck and (b) settings file read by the Python script for post-processing of completed EDEM deck
|
|
|
|
Figure 6: Extracted responses from the EDEM simulation deck
|
|
Multiple simulation decks can be post-processed by arranging files into one of two configurations shown in Figure 7. In configuration two (Figure 7(b)), each simulation deck can be post-processed with its custom setting file whereas in configuration one (Figure 7(a)) a single setting file is read for post-processing of all the EDEM decks. The following sequence outlines the workflow for post-processing.
- Arrange the files as shown in Figure 7.
Open an existing/blank EDEM simulation file and go to EDEM Analyst
Run EDEMpy Script.
Select ‘UCT_analyst_v3.py’
Run Script.
- Reports and graphs will be generated in the master folder.
|
|
Figure 7: Configuration of folders for post processing using the ‘UCT_analyst_v3.py’ script (a) single setting applicable to all EDEM deck, and (b) provision for custom settings for each simulation deck
|
|
Only complete simulations with setting files will be post-processed, otherwise an error message, as shown in Figure 8, will be generated. To avoid file overwriting, all simulation files should have unique folders and simulation names.
|
|
Figure 8: Possible error messages that could be encountered during post-processing
|
|
4. References