Suggestions for Meshing Strategy before setting up model for Casting Simulation
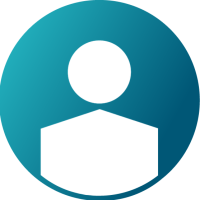
MilanRaval
Altair Employee

Tips and Tricks
Model setup and simulation run can often lead to mesh failure in FEM-based analysis.
- The mesh may fail due to the complexity of geometry or inaccuracies in the definition of imported geometries.
- Since the mesh may fail due to geometry issues. before meshing have a look inside the part (using the section plane tool) to prevent possible future issues.
- Areas with 0 thickness are typical in HPDC hot chamber runners.
- Avoid flash defects (where the two halves of the mold collide) that are not necessary to simulate it and they make the meshes fail because of the very thin surfaces (0.1/0.2 mm).
- Avoid vents air exits, as they may cause problems during meshing because of their thin volume.
- No connection between components. To avoid this issue, push the component to be sure that intersects the part or other component.
- Partial connection between components. To avoid this issue, push the component to be sure that intersects the part or other component.
Summary: Checking all the above points can help the user pass through the mesh failure stage without even facing it. Theses steps are the starter point for any Inspire Cast user who can check potential threats to mesh failure. Inspire Geometry sections allow users to solve these issues without going back to the CAD system. After these target issues are solved, the user can set up and run the simulation smoothly.
1