Ross Point and Wind Up Center Optimization of Leaf Springs Using MotionSolve and HyperStudy
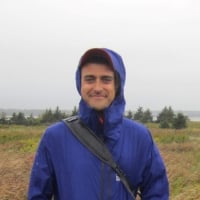

Overview
Preface
Effective leaf spring engineering requires attention to the Wind-Up Center, which is the point where the individual leaves come together and are secured, and the Ross Point, which represents the point of maximum bending stress. Two test rig simulations are required to determine the location of the Wind-Up Center and the Ross Point. These simulations are sequential, such that results from the Wind-Up Center simulation are required to be used as inputs for the Ross Point simulation. This can provide a unique challenge to Users when trying to optimize a leaf spring design as it requires two models and a defined sequence to be effective.
In this article, we detail how we defined a sequential HyperStudy-based process for a Customer to optimize a discretized leaf spring model.
Introduction
A leaf spring is a simple form of spring commonly used for suspension in wheeled vehicles. It consists of one or more narrow, arc-shaped, thin plates that are attached to the vehicle's axle and chassis. This arrangement allows the leaf spring to flex vertically in response to irregularities in the road surface, providing a smooth ride.
The most common configuration is the lateral leaf spring, which runs the length of the vehicle and is mounted perpendicular to the wheel axle. However, there are also numerous examples of transverse leaf springs, which are oriented across the width of the vehicle.
The flexibility of leaf springs helps to absorb shocks and dampen vibrations transmitted from the road. Their simple, robust construction makes them a reliable and cost-effective suspension solution, especially for heavier vehicles.
The leaf spring Wind Up Center (WUC) plays a critical role in ensuring the suspension system can provide a smooth, comfortable, and stable ride quality. Proper design, installation, and maintenance of the WUC are essential for optimizing the performance and longevity of a leaf spring suspension.
The leaf spring Ross Point (RP) represents the point of maximum bending stress, which is a critical design consideration for ensuring the durability and reliability of leaf spring suspensions in vehicles. Proper analysis and attention to the RP is essential for effective leaf spring engineering.
To determine the location of the Wind-Up Center, a torque is created by applying a force to the bottom of a jack. Once at rest, a measurement is taken from the WUC to the upper leaf surface.
To determine the location of the Ross Point, the WUC starting (P1) and ending position (P2) is recorded to used to find the arc center or Ross Point:
In addition to the Ross Point, the Ross Line Length and the Ross Line Angle are calculated to gather all of the necessary outputs to this sequential simulation.
Usage/Installation Instructions
Modelling Details
MotionView Model
The parent model for this analysis is no ordinary leaf spring model. Although it started out as a model generated from the Leaf Spring Tool, the leaves were discretized and parameterized to allow for automated modification of various thicknesses, nominal loads, and coefficients.
Each discrete part of the leaf spring consists of several bodies connected by a beam element.
With this parameterized and discretized configuration, the entirety of the leaf spring model can be optimized for given targets.
HyperStudy Model
The WUC and RP analyses were originally run from within MotionView to confirm the operation of the simulation and the accuracy of the results. The act of running those simulations produced 2 snapshot MDL files, which are essentially a save point of the MDL prior to producing the MotionSolve solver deck. Both snapshot MDLs are used as model inputs for the HyperStudy setup:
In the sequence tab, it was specified that the RP simulation must come after the WUC simulation:
The initial implementation of this sequential optimization only focused on the thickness factors for both leaves. The thickness factors were linked together so each leaf would have the same thickness coefficients, however this could be removed later to explore further options for leaf spring configurations.
In the links tab, we can also see that the X and Z coordinate for the Wind-Up Center point (shown as wuc_mod_cx-value and uc_mod_cz-value) are linked to an output response. This output response is a measurement of the last position of the Wind-Up Center from the Wind-Up Center event. This promotes the sequence where the WUC simulation is completed first, post processed, and then that output response is used to influence the RP simulation. In order to complete this link, the output response must be defined first, then the link can be established.
A series of Data Sources must be defined to extract the necessary simulation data for the Output Responses. In this example, a total of 165 data sources are defined to get access to marker locations, target spring rates, and the torques between each discrete leaf spring section for both simulations.
The Data Sources are then referenced in 68 Output Responses to eventually calculate the initial and final positions of markers, maximum stress, spring rate, and arc centers, etc.
The optimization is then set to minimize 3 objective functions: leaf 1 maximum stress, leaf 2 maximum stress, and the error between the goal spring rate and the current spring rate.
This HyperStudy process in combination with the modular MotionView leaf spring model is an effective modeling and optimization strategy. The modular model allows for a single parent model to be used for all 2 leaf configurations with various dimensions and thicknesses. The sequential optimization is an efficient way of optimizing a system that requires a complex setup.
By applying these principles to your next leaf spring design project, you can save valuable time in the design, evaluation, and refinement of your model by using this modular approach and sequential optimization process.
Hopefully this process can be of use to you in your HyperStudy and MotionView journey!
Post-Requisite
Note: Files used for this article are accessible upon request
Helpful Links
Looking for more material on MotionView/MotionSolve and HyperStudy? Check out our available eLearning courses linked below!