Dynamics Coupling Interface - Swing Door Example
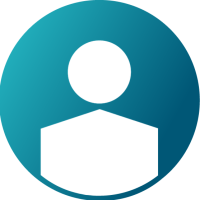

Overview
In this example a simple flop gate is simulated using the EDEM Multibody Dynamics Coupling Interface. The rotational speed of the gate is controlled by the force of particle impacts, producing a torque at the hinge, which is added to the torque from the weight of the door.
What you will learn from the model
Understand how the point of action is used in EDEM to perform rotation from a point different than center of mass
Basic model to see the interaction between particles and geometry
Good introductory model for beginners
Usage/Installation Instructions
Using the EDEM Multibody Dynamics Coupling Interface this simple system can increase in complexity by adding damping due to friction in the hinge, or a more sophisticated method for flow control, such as actuators.
This model is an easy example suitable for beginners with little experience in C++ and/or the EDEM Multibody Dynamics Coupling Interface.
In this example the center of rotation of the door is not at the center of mass. In the EDEM Multibody Dynamics Coupling Interface the point of action for rotation can be specified seperately from the center of mass. This allows easier coding for controlling the dynamics in geometries with a joint or hinge located in a different location than the center of mass.
By default the point of action of the rotation will be the same as the center of mass but with:
coupling.setGeometryPointOfAction(door.id, door.pointOfAction );
The user defines the point of action, which is the point where the torque will be calculated by EDEM and also where the rotation of the body will occur. In this model there is no translation of the geometry to reduce the amount of calculation.
A simple test to validate the model was done using a door with mass 156 kg, dimensions 1m x 1m x 20mm. measuring the angle between the calculated numerical solution and the solution provided from the dynamics. Below you can see the comparison of the results and the starting position with an angle of -90 degrees:
After the validation of the model a simulation with particle-geometry interactions was created where a flap gate is opened due to the force of the falling particles. The gate’s response varies, depending on bulk velocity, bulk mass flow rate, material properties or size distribution.
Such gates, which swing freely on a hinge, can control the mass flow rate, deflect the bulk flow to a new trajectory, and prevent injury from uncontrolled discharge.