Crankshaft and Connecting Rod Validation for a V6 Hybrid Power Unit in MotionSolve and Twin Activate
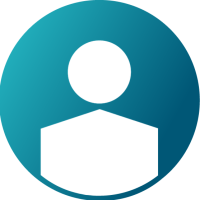

Overview
Introduction
Hybrid vehicles serve as a bridge between the long-range, reliable internal combustion engine and the efficient, environmentally friendly electric motor. While adopting many strengths of both, hybrid vehicles also create new challenges. These hybrid power units must be validated to ensure performance meets requirements and the components are safe from failure. Key components such as the crankshaft, connecting rods, and engine block must be able to withstand the forces of both the internal combustion engine and the electric motor. Multibody dynamics (MBD) provides an accurate, cheap, and quick method for analyzing a hybrid system (or individual systems).
Engineers can use multibody dynamics to predict the dynamic loads on key components during operation. These loads can inform finite element analysis to predict stress hotspots and failure modes. MBD allows the analysis of noise and vibration of a hybrid system. Using the frequencies identified by MBD, engineers can design solutions to eliminate unwanted noise and maximize rider comfort. Finally, MBD can be integrated with 1D control models to optimize control algorithms, allowing engineers to test various strategies and achieve maximum performance.
Building the V6 Model
MotionView
The multibody dynamics model is built in MotionView, an easy-to-use multibody dynamics pre-processor.
- Import IC engine geometry into MotionView.
Figure 1: IC Engine Geometry
- Create bodies for each graphic.
- Create points and joints to connect the bodies.
Figure 2: View of the Joints Connecting Each Body
- Create forces to represent the gas forces, the electric motor torque, the resisting torques from auxiliaries, and a torsional damper to represent external resistance.
- Use FlexPrep to create flexible bodies for the crankshaft and connecting rods.
- Change the crankshaft and connecting rod bodies to flexible and select the .h3d files created with FlexPrep.
Figure 3: IC Engine MBD Model with Flexible Crankshaft and Con Rods
- Create solver variable inputs and outputs to prepare the MBD model for co-simulation with Twin Activate.
Inputs:
- Gas Forces
- Electric Motor Torque
- Auxiliary Torque
- Throttle Position
Outputs:
- Crankshaft Angle
- Crankshaft Velocity
Twin Activate
Twin Activate is a 1D modeling tool specializing in controls systems and physics. Twin Activate will handle the calculations for gas forces in the IC engine, electric motor torque, and auxiliary torques.
Figure 4: Twin Activate Model
Internal Combustion Engine: A 3D lookup table takes in the throttle opening, crankshaft velocity, and phase of the cycle to find the pressure on the piston. The pressure is used to calculate force, which is sent to the MBD model.
Electric Motor: The electric motor duty cycle is defined as the power produced by the electric motor. The power from the motor and velocity of the crankshaft are used to calculate the contribution of torque from the electric motor.
Auxiliaries: A lookup table is used to find the resisting torques created by the auxiliaries based on the speed of the crankshaft.
The gas forces and torques are sent to the multibody dynamics model. The MBD solver uses the boundary conditions to calculate the forces and kinematics of all modeled engine components. Crankshaft phase and velocity are sent back to the Twin Activate model for the next timestep.
Pre-Requisite
Software Requirements
MotionView (2024 or newer)
MotionSolve (2024 or newer)
Twin Activate (2024 or newer)
Model Files
V6_Hybrid_Power_Unit.zip (See attachments)
Usage/Installation Instructions
Running the Model
- Open V6_Controls.scm in Twin Activate.
- Select Run.
- Review the results.
- Open the .h3d file in a session of HyperView to review IC engine motion and component stresses.
- Open the .plt file in a session of HyperGraph to plot key performance indicators.
Post-Requisite
Results
After finishing the simulation, the forces on each body can be animated. Figure 6 shows the stresses experienced by the crankshaft and connecting rods. Hotspots like those shown in Figure 7 can be used to inform fatigue analysis.
Figure 5: Engine Motion and Gas Forces
Figure 6: Crankshaft & Connecting Rod Stresses with Piston Forces Displayed
Figure 7: Connecting Rod Hotspots for Fatigue Analysis
Engine performance metrics like power, torque, velocity, and more can be plotted in HyperGraph.
Figure 8: External Engine Load
Figure 9: Engine RPM
Figure 10: Throttle Position
Figure 11: Electric Motor Torque
Figure 12: Piston Forces
Figure 13: Piston Stoke from 0.80 to 0.82 Seconds
Figure 14: Piston Forces from 0.80 Seconds to 0.82 Seconds.
Forces on the engine block can be measured in the multibody dynamics model. The force of one of the main bearings is shown in Figure 15. The frequencies the crankshaft and engine block will vibrate at can be found by processing the data and taking a Fast Fourier Transform. The FFT results are shown in Figure 16.
Figure 15: Bearing Force on the Engine Block
Figure 16: FFT of the Bearing Force
Conclusion
Multibody dynamics is a powerful tool for validating system performance. In combination with 1D modeling, multibody dynamics can predict the stresses on engine components critical to IC engines or hybrid systems. Results can be used to identify the frequencies of the forces acting on the engine components. Engineers can use this information to design solutions to dampen undesirable vibrations and improve rider comfort. Finally, engineers can test different electric motor control strategies to maximize hybrid engine performance while validating critical components.
Authors
John Dagg, Systems Engineering Intern
Christopher Fadanelli, Solution Engineer – Systems Integration
Ananth Kamath Kota, Global Technical Manager – Systems Integration