Intrinsically Linear Functions to Improve Fit Quality
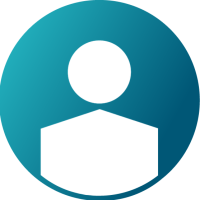

When creating a fit you often get the best results when there is a linear relationship between the design variables and the responses. When this is the case Linear Regression will give a perfect fit, barring any noise in the data. Although fitting methods such as Radial Basis Functions, Gaussian Process or Moving Least Squares can capture non-linear behaviour, more training points are required to do so. When considering multiple design variables, the number of required training points is further increased.
There are many functions which on first glance do not look linear, but with a transformation, can be made to do so. These are called intrinsically linear functions. Some examples of these functions and the transformation required to make them linear are shown below.
These sorts of relationships are seen in many different engineering equations. A very simple example of an inverse relationship can be seen in structural analysis with the relationship between stiffness (k) and displacement (u). Consider Hooke’s law where force ( F ) is defined as:
Which may be rearranged to give displacement and stiffness respectively as,
and
If the force is a unit load the relationship between stiffness and displacement becomes,
and
.
As a practical example of how this relationship can be used to improve fit quality, consider the following simple example of a plate which is fully constrained on one side and pulled on the other with a unit load. The gauge thickness of this plate is then varied as a design variable and the displacement at the loaded end is evaluated as the response.
The relationship between the gauge thickness and the displacement response and corresponding Linear Regression fit is shown below.
Although the Linear Regression fit captures the trend, there is a curve in the data which is not captured. If instead the displacement was converted to stiffness, using the previously derived equation, and plotted against the gauge thickness the following relationship and fit is seen.
The linear regression perfectly models the data. A prediction of the displacement can now be obtained by first predicting the stiffness then transforming it into displacement, as shown below.
The linear relationship between the gauge thickness and the stiffness is explained by the stiffness equation,
Where E is Young’s modulus, L is the length, and A is the cross sectional area calculated from the width ( w ) and the gauge thickness ( t ). The relationship between stiffness and the gauge thickness is given by
As Young’s modulus, width and length are constant the relationship between stiffness and gauge thickness is shown to be linear, as observed in the graph above.
Although this was a very simple example of the power of intrinsically linear functions, there are many engineering problems that can make use of them. These can be identified by using engineering knowledge or performing investigations into the design variable – response relationships before embarking on an optimization study. This can lead to better quality fits for a lower number of required training points, improving accuracy whilst reducing the computational effort required to perform a study.