Altair Inspire® Challenge #1: Bridge Concept Design
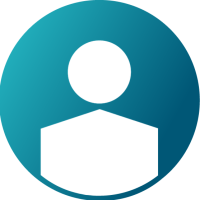

Have you ever looked at a bridge, and wondered what factors determine the ideal support system for such a structure?
Now is your chance to use Altair Inspire to help answer that question.
In this challenge we have a scaled down bridge, for which we want to determine the preliminary structural layout. The bridge deck must remain intact, but the supporting structure (under, or even over, the deck) can be optimized using topology optimization.
The structure must be able to support its own weight, plus the applied loads in the model. The goal is to minimize deflections, and eliminate redundant material. You may use the provided design space, or create your own. Ensure that the structural layout does not obstruct vehicle movement across, or underneath the bridge.
Tip: If you have trouble running an optimization, try running an analysis to ensure the model is behaving as expected.
Level: Easy
Product Required: Altair Inspire (including personal edition)
If you would like to solve more challenges and get regular challenge release updates, Subscribe to the Altair Community Challenge forum.
Edit: A solution to this challenge has been attached as an image file using the original optimization settings in the file. Try to solve it on your own before looking at it! Note that this problem is intentionally open-ended, so your solution may not match exactly, and that's ok. Perhaps yours is even more efficient!
Comments
-
Hmm. Am I doing it right? I cant run it like that? Should I be able to run it like that or should I do something( and that is the challenge? )?
1 -
Karli said:
Hmm. Am I doing it right? I cant run it like that? Should I be able to run it like that or should I do something( and that is the challenge? )?
Hi Karli, you may need/want to modify the design space and run settings to come up with a unique design. I'm afraid I cannot give too much away without spoiling the contest as it is meant to be open-ended, but if you continue to have troubles please let us know. Can I ask, were you able to run an analysis on your model?
1 -
Interesting assignment.
.
Couldn't able attach a .stmod file larger than 15Mb
1 -
Greetings everyone, in the event that you encounter difficulties attaching a .stmod file, kindly share the optimized solution by attaching a JPEG image instead.
Regards,
Sourav
3 -
Hello!
I ran a simple optimization and it looks curious, reminds me of trees somehow due to its shape! As objective, it reduced 65% of volume and went from 119kg of steel to 62.8kg. It mantained deflections on ranges of maximum 156nm, which I would think is acceptable. Surely there are better ways to optimize it!
1 -
David Galvis_21599 said:
Hello!
I ran a simple optimization and it looks curious, reminds me of trees somehow due to its shape! As objective, it reduced 65% of volume and went from 119kg of steel to 62.8kg. It mantained deflections on ranges of maximum 156nm, which I would think is acceptable. Surely there are better ways to optimize it!
Very nice, David! Thank you for your submission, we will be reviewing the submissions in the coming days and selecting the winner so please stay tuned!
0 -
Kunal Pandit_21294 said:
Interesting assignment.
.
Couldn't able attach a .stmod file larger than 15Mb
Hii,
The concept for this bridge is used on big rivers joining two shores. A simply supported bridge is constrained on both ends. 10 tons of force is applied on the surface for vehicle load.
The mass reduction seen before and after topology optimization is 22,821,000 kg. The maximum displacement seen is 1.639e-02 mm.
Thanks.
1 -
Kunal Pandit_21294 said:
Hii,
The concept for this bridge is used on big rivers joining two shores. A simply supported bridge is constrained on both ends. 10 tons of force is applied on the surface for vehicle load.
The mass reduction seen before and after topology optimization is 22,821,000 kg. The maximum displacement seen is 1.639e-02 mm.
Thanks.
Very nice, Kunal! We'll be reviewing the submissions in the coming days, so please stay tuned.
0 -
Here's what i got.
1 -
Ripfumelo said:
Here's what i got.
Very nicely done, as always! Thanks for your submission!
1 -
Karli said:
Hmm. Am I doing it right? I cant run it like that? Should I be able to run it like that or should I do something( and that is the challenge? )?
Now I did try it again. There was still some problem, because the object materials where "materila 4". Was it supposed to be like that?
Anyways, I changed the material to steel (S355) and it worked:
only 0.00028 mm displacment.
1 -
Karli said:
Now I did try it again. There was still some problem, because the object materials where "materila 4". Was it supposed to be like that?
Anyways, I changed the material to steel (S355) and it worked:
only 0.00028 mm displacment.
Thanks, Karli! It looks great. On our end, we were able to run with the default material, but it could obviously be adjusted at your discretion.
1