Flowrate and Pressure Boundary Conditions in Altair Flow Simulator
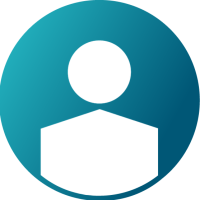

Flowrate and Pressure Boundary Conditions
Flow Simulator has the flexibility to specify flowrate or pressure boundary conditions. The choice depends on what information is known and what results the model should return. The 3 simple networks shown below illustrate the 3 different types of boundary conditions available.
- Inlet Pressure and Outlet Pressure. Use this option when the pressures are known, and the flowrate is unknown.
- Inlet Flowrate and Outlet Pressure. Use this option when the flowrate and outlet pressure are known, and the inlet pressure is unknown.
- Inlet Pressure and Outlet Flowrate. Use this option when the flowrate and inlet pressure are known, and the outlet pressure is unknown.
The fixed flowrates in networks 2 and 3 were set to the same flowrate as network 1 to illustrate that the same pressures are obtained in the internal plenum chambers (14 bar upstream and 10 bar downstream of the Advanced Tube element).
These 3 models can be used to answer different questions about the advanced tube element. Model 1 can be used to find the flowrate in a tube with 14 bar upstream and 10 bar downstream. Model 2 obtains the upstream pressure required to flow 2.046 kg/s through a tube with 10 bar at the exit. Model 3 calculates the downstream pressure needed to flow 2.046 kg/s through a tube that has 14 bar upstream.
Remember this when using fixed flow elements:
- The boundary chamber attached to the upstream end of a fixed flow element should have an accurate temperature defined since the temperature is passed through a fixed flow element to the downstream chamber.
- The pressure on the boundary chamber at either end of a fixed flow element is not used by the FS solver, but it is used by the internal flow chamber initializer in the GUI. So, try to put a reasonable pressure on the boundary chamber even though it will not matter to the final solution. This pressure will affect the initial guess.
- If the flowrate is too high, the FS solver may have trouble converging. A flowrate higher than the choking flowrate of elements in a compressible gas network will be a problem. Very high pressures or very low static pressures (cavitation) may be obtained for an incompressible network with very high fixed flowrates.
More About Fixed Flow Elements
The fixed flow element does not have to be used at the ends of a network. It can be used anywhere along a series of elements. Just don’t put multiple fixed flow elements in the series unless they are given the exact same flowrate.
A fixed flow element is also a good substitute for a pump element during system design. Use a fixed flow element with the target flowrate at the location of the pump in a network. If the fixed flow element is attached to 2 internal chambers, the pressure rise required by the pump can be calculated using the chamber pressure results.
The flowrate in a fixed flow element does not have to be a constant. A controller can be used to change the flowrate based on time or other items in the flow network.