Effect of Surface Roughness on mmWave Design Antenna Arrays
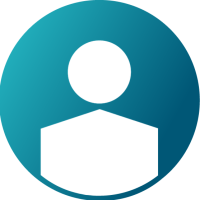
In the past decade, applications that use millimeter (mm) wave frequencies (30-300 GHz) have increased significantly to facilitate very high data rates and wide operational bandwidth. However, designing circuits and antennas at mm wave frequencies pose a challenge of its own. One such factor is surface roughness, which affects the conductivity of the metals used in the design and leads to degradation of performance.
Surface Roughness
Surface roughness, often shortened to roughness, is a component of surface texture. It is quantified by the deviations in the direction of the normal vector of a real surface from its ideal form. If these deviations are large, the surface is rough; if they are small, the surface is smooth. Surface roughness can be controlled using advanced and precise manufacturing techniques; however, they can be expensive. So, it is important to study the effect of surface roughness while designing mm wave circuits and antennas to avoid expensive modifications later in the design stages.
In this blog, we consider one such application of automotive cruise control (ACC) radar that operates at 76.5 GHz and study how various values of surface roughness affect different performance parameters of the design. This study makes comparisons are by evaluating key antenna performance parameters by considering Perfect Electric Conductor (PEC), and copper with various values of surface roughness. All the simulation results presented in this study are obtained using Altair Feko.
Array Design
A microstrip array that consists of six single columns is considered for the design. Each column has ten individual radiating patch elements that are connected with a strip line feed. The substrate used has relative permittivity of 2.35 and dielectric loss tangent of 0.004. Planar multilayer Green’s Function option in Feko is used for analysis of the antenna. The dimensions of individual patch elements are optimized to achieve good matching with 50-ohm reference impedance and required side-lobe-level. The conducting patch elements are initially set to PEC as a base line. Later, the simulations are conducted with copper of 35μm thickness with and without surface roughness values. The 3D radiation pattern of the antenna array is as shown below-
For more details on effect of surface roughness on parameters like losses, gain and efficiency, please read the attached conference paper. A video that describes the study is also attached to this blog. For more details, please reach out to Altair Support.
https://www.youtube.com/watch?v=NJvB6ca4LoI