Growing Companies Need PCB Verification in Their Workflow
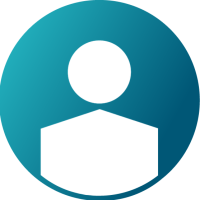

Managing a growing team effectively can be done only by developing best practices and a process workflow. As the size of a company grows, more engineers are needed to work on the different projects. Having a strong workflow allows you to improve execution, knowing there are process checks and reviews required. A strong workflow also allows new engineers to become less reliant on a subject matter expert for a question. This gives the expert more time to focus on the tough, critical issues.
To efficiently build electronic devices, a strong PCB workflow must be established.
One of the first things a growing company can implement is a verification step into their workflow. A company’s first product design will contain many revisions due to bug-fixing the designs. That time is also spent learning best practices while building competence. Over time, future designs leverage this knowledge to make the next design more efficient. Does your team have a verification step to make sure best practices are being implemented in future designs?
Figure 1: An example of a PCB verification workflow
Including a dedicated verification step in a design process takes the knowledge of previous revisions and puts them into a document that serves as a check list of items to review. Verification for PCBs are performed before a PCB is released and signed off by the team leads and/or the pre-production quality engineer.
One way to incorporate verification for PCBs is to check that the board has met requirements established by the team before it is released to manufacturing. Another way to incorporate verification is to create a rule-based checking system that all PCBs must comply with to ensure a high-quality product. Implementing verification will pass along the knowledge that was learned while designing the initial revisions. It’s hard to keep track of best practices when different engineers work on each product, since each engineer will have their own design style. Each engineer is also capable of making mistakes that will reappear as functionality or mechanical defects. Adding verification helps to save time by reducing the number of rebuilds of a PCB. This also saves money since costly components are scrapped when a fully assembled PCB fails quality checks.
Using verification can help find issues before the PCB is assembled.
To improve your company’s verification process, try implementing verification software into your workflow. Verification software can automate the process of setting up the rules and creating design standards. Using verification software allows you to check that every PCB complies with hundreds of rules without having to hand check each rule. You can also incorporate the nuance of product use cases by creating special rules depending on the component or net name. The results will be in the form of a pass / fail list based off the measured value, and the results can be presented easily for sign off or discussion. Using verification software also allows you to only focus on the areas of concern. This saves the engineer’s time, including the engineering guru that can focus on the critical issues. Software-based verification for PCBs is growing in adoption for large companies that have multiple engineers designing PCBs. There are three main areas of verification for PCBs:
- Design for Electrical (DFE) verifies that PCB connections are correct while also accounting for spacing to other components or the board edges. Component clearances and other electrical checks can also be helpful to design for electromagnetic compatibility (EMC) or to avoid electrostatic discharge (ESD) events.
- Design for Manufacturing (DFM) verifies the PCB can be manufactured based off the equipment and tolerances a PCB manufacturer provides. Challenges with technical cleanliness and other issues can be avoided through DFM checks.
- Design for Assembly (DFA) verifies that the components and other additions on a PCB can be soldered or placed on the PCB with no errors.
Combined, DFE, DFM, and DFA are referred to as a single term: DFx, or Design for Excellence.
Altair provides DFx coverage for PCBs through our Altair® PollEx™ solution that helps to automate the verification process. This solution is widely used by leading global electronic players, including Samsung and LG Electronics. Our resources can help an engineering team implement their first verification process in hours, resulting in a workflow that improves the quality of all products. The verification process can be improved over time to align to the nuances of the growing company. To learn more, we recommend you watch Pollex in action for DFM in this short video tutorial. More information and other video tutorials can be found in our Resource Library.