Strategic Decision Making in Manufacturing with Digital Twins
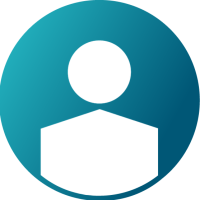
The Challenge
In the metal forming industry, simulation of processes and the resulting material behavior has become a highly valuable standard practice. The investigation of key process parameters - such as material flow, temperature range, required press tonnage, as well as resulting material characteristics including strength, residual stresses, and thinning - has been supported for quite some time by finite element analysis (FEA) simulation, replacing costly physical tryouts.
The knowledge gained from simulation can now be combined with data acquired from sensors on the actual press and tooling. This information can be tracked on generated dashboards that show key performance indicators (KPIs). Simulation methods like this provide manufacturing teams with valuable insights on ever-varying process conditions and support strategic decision making.
A good example of such an approach is a recent digital twin implementation using Altair’s software toolset and technical expertise at Patrone e Mongiello (PM Gruppo), an automotive supplier of metal stamped parts, located in Europe (Italy and Poland).
PM Gruppo’s engineers were facing two very practical – yet very concerning – challenges: first, every time a new material coil was loaded for the production, even before starting producing parts, they needed at least one day to modify and re-calibrate the machine parameters. This was causing a huge loss of money since they had a few press machines of the same type, hence the need to avoid unexpected stops of the processes for the onset of anomalies.
Second, and equally important, production malfunctioning caused material microfractures in some critical points on the finished pieces. This led to increased production time and costs to make up for the lack of quality. As a result, PM Gruppo wanted to improve the efficiency and the effectiveness on quality of the produced components.
Our Solution
Relying on machine learning (ML) algorithms using reduced order modeling (ROM) and advanced data visualization, Altair worked with PM Gruppo and our partner Advanced Engineering Solutions to build a digital twin platform that provided a holistic view of the entire manufacturing process through an IoT-based dashboard that combined visualization of actual data and derived KPIs.
Analyzing the evolution of dimensional and process parameters during production allowed the customer to quickly make strategic decisions, evaluating the impacts of – as an example – a batch of material with different characteristics or varying blankholder pressure, enabling corrections to production parameters in real time.
The Results: 15% Waste Reduction and Runtime Slashed from Hours to Seconds
The outcome of the process has been an increased efficiency and environmental sustainability of processes and metal formed products via the integration of the digital twin into the company’s digital factory IT architecture. More specifically, PM Gruppo experienced over 15% reduction of production waste, while the run time for operations such as loading a new material’s coil was reduced from hours to seconds.
Most importantly, a comprehensive, accessible, and open data processing infrastructure has been set in place, enabling quick corrective actions and production alerts to take place on the shop floor.
The Future
Altair provides the most comprehensive digital twin solutions, comprising best-in-class technologies that can be seamlessly integrated into established workflows. Additionally, Altair offers domain expertise—people! Indeed, beyond delivering software, Altair is foremost a company comprised of skilled individuals at your disposal to help you achieve your goals more efficiently!
The upcoming ATCx Digital Twin 2024 event by Altair taking place virtually on October 17, 2024, is an essential opportunity for engineering professionals to delve into the core of digital twin technology and engage with industry leaders in simulation and product design.
Don’t miss this chance to advance your expertise and network with top professionals. Register now to secure your spot and be a part of the future of digital twin technology.