Shape Optimization of Excavator Bucket
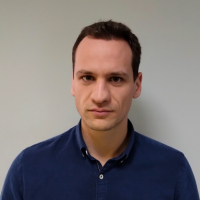

(This is a translated version of a blog posted by Kosuke Ikeda. The original blog in Japanese can be found here).
In this blog, we discuss a workflow to find the bucket shape that optimizes the particle filling process during an excavator digging cycle.
The simulation of this process is done using Altair Inspire parametric design and a co-simulation between MotionSolve and EDEM. The process of changing the bucket shape and running the new simulations can be time consuming so here HyperStudy is leveraged to automate the workflow.
Finally, the optimization for the shape parameters is done with the help of a reduced order model created with Altair's romAI.
As a result, we were able to find a bucket shape that achieves a 20% performance improvement in terms of filling capacity.
Parametric Modeling with Altair Inspire
Altair's Inspire sketching and parametric features allow you to easily create a parametric bucket shape.
With the parametric design we can quickly vary the bucket shape just by changing the parameters as shown in the video bellow.
Excavation Simulation with Altair MotionSolve and Altair EDEM
By leveraging the native co-simulation ability between Altair MotionSolve and Altair EDEM, we can simulate the full multibody excavator (including flexible components) interacting with the granular material / particles.
Altair MotionSolve is multibody analysis software that allows you to simulate the dynamic behavior of moving machine, in this case an excavator. Elastic deformation can also be considered with flexible bodies exported from OptiStruct. Thus, it is possible to evaluate the stress and strain of the arm and the boom during the excavation process.
In combination with the 1D simulation tool Altair Twin Activate, the hydraulic actuators and control systems can also be integrated to perform the full systems simulation.
Altair EDEM is a Bulk material simulation software based on the Discrete Element Method that gives a crucial insight into how those materials will interact with their equipment during a range of operation and process conditions. A variety of material models, such as General EDEM Material Model and Soil Starter Pack / Powder Starter Pack are available, allowing you to perform simulations easily.
DOE by Altair HyperStudy
Altair HyperStudy is DOE and optimization software to automate the simulation steps / workflow.
For this example, we utilize the additional EDEM-HyperStudy Connector to run a design experiment varying the bucket shape.
During each run of the DoE the Inspire parametric model automatically updates the bucket's geometry and feeds it into the MotionSolve-EDEM co-simulation. After the simulations have completed, the digging cycle metrics can be extracted, such as the maximum reaction force, the energy required to perform the movement, and the mass of particles that remain on the bucket after the cycle (filling quantity).
High Performance Computing (HPC) with Altair Unlimited
Altair EDEM has a fast and scalable solver optimized to run on CPUs and GPUs which can be further accelerated using Altair's cloud environment, Altair Unlimited.
The EDEM-HyperStudy Connector also supports the ability to submit the DoE jobs in the Cloud (Altair Unlimited) and automatically extract the response results/metrics.
To save time, multiple EDEM simulations from the DoE can be performed in parallel on the cloud.
Reduced dimensionality model and optimization by romAI
Using the DoE results from HyperStudy as training data, Altair romAI can be used to create a Reduced Order Model leveraging AI.
The ROM generated can predict the filling performance based on the bucket shape parameters as inputs.
So for this example, we run an optimization process in Twin Activate using this ROM to find the set of bucket parameters that maximize the amount of excavated soil (filling mass).
Validating the performance of the optimized bucket shape
Using the bucket shape predicted by the optimization process, we perform a final validation run using the high-fidelity MotionSolve-EDEM co-simulation to confirm the excavation performance.
As a result, we were able to confirm a 20% improvement in the bucket filling mass compared to the original shape.
Software used
Comments
-
On the links bellow you find can more details on the individual steps, as well as the model files
The articles bellow are in Japanese so we suggest you to use the built in browser translator.
How to Create a Parametric Bucket Model in Inspire
How to use EDEMpy scripting to calculate the mass of excavated soil during digging cycle
How to the geometric characteristics on the parametric bucket model
How to automatically reshape a bucket using Altair HyperStudy (without constraints on volume)
How to calculate the energy consumption during the digging cycle
How to set up a DoE on HyperStudy coupling the models together
How to create a reduced order model with romAI and use it for optimization
2