Inspire to Do More | Bracket Parametric Optimization
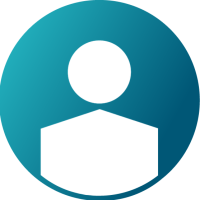

Inspire is a great tool when optimization FOMO isn't causing you to lose sleep. I've been using it for a few 3D-printed DIY projects here and there. The CAD tools are serviceable for single parts, and it's easy to run a structural analysis to see if it is actually a good idea to 3D print that bracket. Unfortunately, the proximity of the optimization tools makes for a restless night if you, like me, are inclined to optimize the last 3 ounces off your part.
My sleep paralysis demon takes the form of a small bracket used to attach a PVC L-trim to the bottom of my paddle board. LED strips will be glued to the L-trim. The bracket has holes for nylon straps to pass through and buckle around the paddle board. The system ensures the underside of the board will be lit up so nearby vessels can see me during nighttime rides. Good analysis results ensure that I sleep the night before.
Cross-section view of Paddle Board. Me not to scale.
The bracket was designed with the CAD tools in Inspire. The L-trim will be glued to the bracket through the L-shaped hole in the center. Holes for the nylon straps are at either end of the bracket. Design variables were added to parametrically set the dimensions of material around the strap hole and these will be used later for optimization.
CAD review with variables.
OptiStruct in Inspire was used to analyze the bracket. The part is loaded by forces to match the rated tension of the nylon straps (55 lbf). It is fixed where it glues to the L trim. A mesh size of 0.025 in was used to get a few elements in the fillet region. Initial results showed a questionable factor of safety around the inside of the hole and on the outside of the part.
Initial analysis results. Factor of Safety beneath 1.5 is shown.
It was after running this simulation that I saw it was my bedtime and I had to go to "sleep".
Sleep?
Thankfully, the next day I was able to revisit the problem with Inspire's Design Explorer Optimization. Since I already had the variables set up, it was trivial to run the study. I set bounds for my design variables, a constraint of 1.5 FOS, and a minimize mass objective. The design explorer modified these variables for me automatically to run a bunch of studies and see which one best met my constraints and objective. See the video at the bottom of this blog post for my complete workflow.
Design Variable bounds for my optimization study.
The study finished 20 runs with Multi Execution = 2 at 14.5 minutes on my laptop. For giggles, I also ran this study in SimSolid with 4 passes and adapt to features/thin solids and it finished in 11.5 minutes. I didn't care to do a convergence study between the solvers but both runs pointed to maxing out the Inset and Height. SimSolid got higher stresses in the fillet and recommended a slightly bigger BracketLength.
In the Results Explorer browser, I could see the results of all my runs and review the optimal design! This one clearly meets my minimum FOS so I should be able to rest easy. Off to the printer, this design goes!
Results Explorer Browser and final analysis results. Factor of Safety beneath 1.5 is shown.
Final analysis results with no isosurface.
The final design, 3d printed and test fit to the L-trim.
Video of my Workflow:
[0:40] CAD and Variable Setup
[2:40] Baseline Analysis
[3:50] Design Explorer Setup
[6:30] Reviewing Optimization Results
https://www.youtube.com/watch?v=99Ffwfj6ODY
Relaxing with the sunset