What's new in Altair OptiStruct 2023?
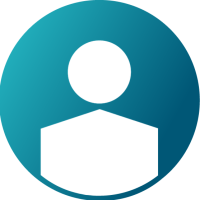

Continuing to build on more than 25 years of innovation, Altair OptiStruct™ is used globally by industry-leading companies to drive design with optimization and validate structural performance.
The latest release of Altair OptiStruct™ - Altair's optimization-enabled structural analysis tool - now offers extensive capabilities for Contact Wear output, Beam plasticity, and support for Dynamic Stiffness output. It also continues to add significant enhancements in Explicit analysis, such as Continuum Shells. It additionally includes significant Optimization enhancements, along with continued improvements to Heat Transfer analysis.
OptiStruct in a nutshell
OptiStruct solves both linear and nonlinear problems across static and dynamic, vibrations, acoustics, fatigue, heat transfer, and Multiphysics disciplines. With its topology optimization driving lightweight, structurally efficient product design today, OptiStruct also offers many other structural optimization methods, along with a broad range of essential manufacturing constraints for traditional processes, composites, and additive manufacturing.
New to OptiStruct? Find out more here: https://www.altair.com/optistruct-applications/
Join the OptiStruct Community https://community.altair.com/community?sys_id=0204add61b9d0c50a028542d1e4bcb9a&view=sp&id=community_topic&table=sn_communities_topic#products
In this post, we will focus on some of the enhancements in OptiStruct 2023.
Implicit Nonlinear Analysis
Implicit Nonlinear analysis features continue to be aggressively improved in OptiStruct. A new implicit nonlinear analysis feature in OptiStruct 2023 is:
Wear Output
Wear Output capability is now available to predict wear, for example, metal to metal wear, for frictional continuous sliding contacts. It is supported for both Nonlinear Static analysis and Nonlinear Transient analysis.
The Wear is calculated based on the Archard Wear equation, and you can define parameters such as wear coefficient, hardness, and exponents.
Explicit Dynamic Analysis
Significant improvements and enhancements are made to Explicit Dynamic Analysis in OptiStruct to provide you with the most cutting-edge technology for various applications. A couple of new features added in OptiStruct 2023 are:
1D Beam Plasticity
Integrated beam cross-sections are now available for ROD and BAR type PBEAML beams. This is supported for both implicit and explicit nonlinear analysis. This is supported for isotropic, kinematic, and mixed hardening (MATS1).
Integrated beams are based on Timoshenko theory and are applicable to short and slender structures. Plasticity is considered for axial and bending deformation. Explicit analysis additionally considers plasticity due to shear strains as well.
Continuum Shells for Explicit Analysis
Continuum shells utilize 3D solid element topology with associated displacement degrees of freedom and they are now also available for Explicit analysis. They are use-friendly elements for bending problems, coupling with classical solid elements and double-sided contacts.
Continuum shells work as Mindlin-type shell elements and additionally consider changes in thickness direction. Kinematic equations are based on shells and constitutive (material) relate to 3D solids. The element formulation combines the assumed strain with reduced integration to remove locking.
Noise Vibration and Harshness (NVH)
OptiStruct 2023 continues enhancements for NVH by introducing the capability to calculate an important output known as Dynamic Stiffness.
Dynamic Stiffness Output
Dynamic stiffness is a widely used output in the NVH domain, and it is now available as a standard output via the KDYN output request.
Dynamic Stiffness is the reciprocal of the displacement. KDYN output is available in both H3D and PUNCH formats. SORT1, SORT2, and PHASE options are supported for PUNCH format.
Heat Transfer Analysis
OptiStruct 2023 continues enhancements for Heat Transfer by introducing multiple new feature, include the capability to activate auto-timestepping for Transient Thermal Analysis.
Auto-timestepping for Transient Thermal Analysis
Auto-timestepping allows adaptive continuously adjusted time-step control for Transient Thermal analysis. Auto time-stepping calculates the error for each grid that is based on the time-derivative of the temperature and capacitance. This can allow improved performance in many situations.
It is turned off by default and can be activated by setting MREF=1 in TSTEP entry. It is supported for linear (default Newmark-Beta) and nonlinear (default Backward Euler) transient thermal analyses.
Optimization
Altair OptiStruct™ is used globally by industry-leading companies to drive design with optimization and validate structural performance. Enhancements to optimization solutions are implemented for each release and similarly, in OptiStruct 2023 many optimization enhancements are available to you, including the following:
Electrical Optimization
Optimization is now available based on electrical analysis and can be combined with other analysis types. The Electrical Potential (ELPO) and Electrical Compliance (ELCOMP) responses are available for electrical optimization.
Topology, Free-shape, Shape, Free-size, Size and Topography optimization are supported.
Shape Optimization with Elasto-plasticity
Shape optimization considering elasto-plasticity is now available. Plastic strains, Displacements, Mass, and Volume can be used as responses. Shape optimization (DVGRID) and Free-shape (DSHAPE) optimization are supported. For Free-shape, both Classic and VERTEXM methods are available.
It is currently supported for small displacement Nonlinear Static analysis.
Milling Constraints
5-axis milling provides enormous design freedom and enables the fabrication of complicated shapes. To allow the optimization of such parts, milling manufacturing constraints have been added to OptiStruct. They are supported for Topology optimization via level-set method. Milling constraints can only be applied to solid elements.
Milling constraints can be defined in one of two ways, directly defining the ANGLE (D/L ratio) field on DTPL, or by defining the dimensions of the mill bit and head using R, B and H fields on DTPL.
View release notes and download from Altair One https://marketplace.altairone.com/Marketplace?app=OptiStruct