Introducing Industry-Grade Polyhedral Particle Simulation in EDEM 2021
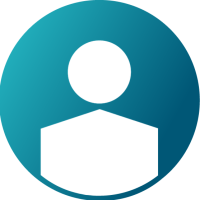

The EDEM team has always recognized the importance of particle shape as a key characteristic to recreate complex granular material behaviors. It is why we led the way with our multi-sphere approach and have been encouraging our users to make use of shape, for the past 15 years. Now in EDEM 2021, we are taking advantage of the latest GPU hardware to extend our particle shape options and introduce an industry-grade polyhedral solver that allows you to address even more applications.
In many industries, DEM is used to replicate the behavior of real-world processes containing billions and billions of individual rocks, grains, or granules. In such cases it is the BULK flow behavior that is of interest and our multi-sphere approach [1, 2] gives you the best balance of accuracy and computational performance.
However, in some applications there are specific shape requirements that can prove challenging for the multi-sphere approach. For example, in cases where you have high-aspect ratio particles such as flat plates, or very uniformed shape particles such as cubes or cylinders. In such cases the multi-sphere method may require large numbers of spheres to represent each particle which can result in an increased computational overhead.
It is these cases that the EDEM Polyhedral Particle Solver looks to make more accessible to our users.
Examples of the EDEM polyhedral solver. [Clockwise from top left] Cubic elements in a mixing drum; flat plates discharging into a container; high-aspect ratio particles in a screw auger.
Overview of the EDEM Polyhedral Particle Solver
When it comes to polyhedral particle solvers the number one topic we hear about is speed. Performance is essential to all our customers and polyhedral-based simulations have a reputation for being significantly slower that sphere-based approaches. We wanted to make sure that our polyhedral solver would be more than just a pretty visualization. By capitalizing on recent advances in GPU hardware, and backed by our team’s strong understanding of developing GPU-based solver technology, our polyhedral solver delivers the type of performance needed to address industry-grade problems.
Comparing performance of EDEM multi-sphere solver vs. polyhedral solver. Numbers indicate the speed relative to single sphere e.g. Tetrahedron is 3.38 times slower than single sphere.
In addition to great performance, the solver also comes with a number of supporting tools and features. Polyhedral particle shapes can be created in the EDEM user interface or imported from CAD software and shapes can have size distributions assigned to allow for the real-world variation in materials. The polyhedral solver can be used with the EDEM Coupling Interface for coupled simulations with CFD, MBD and custom scripts.
Finally, at EDEM we are all about robust validated physics we have implemented a choice of contact models – including the Nassauer Kuna [ref] as default. It is fair to say that the number of publications for polyhedral contact models is smaller than compared to those using the multi-sphere approach, and so our polyhedral is also compatible with our EDEM API solver to enable our wide academic user base to research and develop new contact models for the future.
Comparison of EDEM polyhedral solver vs hopper discharge experiment and paper; Hexahedron particles – based on D. Höhner et al [3]
Multi-sphere or Polyhedral?
The EDEM Polyhedral Solver is designed as an alternative, and not a replacement, for our leading multi-sphere approach. For many bulk materials applications, the multi-sphere approach continues to offer the right balance of computational efficiency and accuracy. However, if you have more precise shape requirements for your specific application – such as those outlined above – then our polyhedral approach is for you.
In fact, you may want to try using polyhedral particles to see how it performs for your application – after all you can always revert to using our world-class multi-sphere solver to ensure you are delivering the benefits of shape in the most efficient way possible.
This is just the start, we will continue to be developing advance this solver and we are excited to see it in action on industrial applications. As always, please let us know hear how you find using it and let us know your feedback and suggestions.
References
[1] M Alizadeh, A Hassanpour, M Pasha, M Ghadiri, A Bayly, (2017) The effect of particle shape on predicted segregation in binary powder mixtures, Powder Technology, Vol 319, pg 313-322, https://doi.org/10.1016/j.powtec.2017.06.059.
[2] W Nan, M Pasha, T Bonakdar, A Lopez, U Zafar, S Nadimi, M Ghadiri, (2018) Jamming during particle spreading in additive manufacturing, Powder Technology, Vol338, pg 253-262, https://doi.org/10.1016/j.powtec.2018.07.030.
[3] D. Höhner, S. Wirtz, V. Scherer, (2015) A study on the influence of particle shape on the mechanical interactions of granular media in a hopper using the Discrete Element Method, Powder Technology, Vol 278, pg 286-305, https://doi.org/10.1016/j.powtec.2015.02.046.