Modeling geometry deformation due to abrasive and erosive wear in EDEM
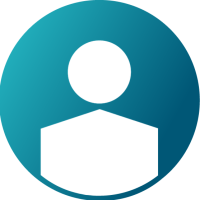

Wear is a ubiquitous and costly phenomenon which can progressively reduce the efficiency of equipment and culminate in its functional failure. Equipment components, which interact with granular materials, can experience particularly high rates of wear, and so an understanding of where wear occurs, how quickly it develops and its effect on equipment performance is key for generating improved designs. Traditionally these questions have been addressed via physical prototyping, which can be slow and expensive. As a result, numerical tools such as Altair EDEM are becoming more widely adopted. EDEM can be used to model the interaction of granular materials and equipment to predict the regions of wear and the wear rate. With the release of EDEM 2020.3 it is now possible to model geometry deformation due to wear via EDEM’s powerful Application Programming Interface (API), and this type of modeling can be used to understand how equipment performance changes as wear progresses. Users can leverage EDEM’s extensive wear modeling features to virtually optimize equipment and generate improved designs cheaper and faster.
The wear of material due to particle interactions can result from a wide range of micro-mechanical phenomena such as cutting, fracture, plastic deformation, impingement, fatigue, and many others. While the complexity and diversity of these underlying phenomena is immense, wear due to particle interactions can be usefully categorized into just two broad categories – abrasive and erosive wear.
Abrasive wear occurs when particles slide against equipment surfaces. This type of wear can be modeled using the classical Archard wear model [1], which is built in EDEM. The model predicts the volume of removed material due to abrasion as a function of normal contact force and sliding distance and requires only one input parameter – an empirical wear constant. The results in EDEM are given in terms of a wear depth on geometry mesh elements which enables the deformation due to wear to be introduced into the simulations. This is achieved by displacing the nodes of the geometric elements on the basis of the computed wear depth using EDEM’s API. A plug-in version of the model with this feature is now available from the Knowledge Base.
Erosive wear occurs when particles impact equipment surfaces. This type of wear can be modeled using the widely adopted Oka wear model [2,3], which predicts the volume of removed material due to particle impact as a function of the particle size, impact velocity, and impact angle. Only two input parameters are required for the model – the Vicker’s hardness of the worn material and an empirical wear constant. The results in EDEM are given in terms of wear depth on geometry mesh elements similarly to the Archard wear model. Plug-in versions of the Oka wear model with and without geometry deformation are available for download from the Knowledge Base.
A comparative analysis of the Oka and Archard wear models was carried out using the EDEM transfer chute simulation shown in Figure 1, where the wear of a deflector plate is of interest.
Figure 1 EDEM simulation of particle flow on a transfer chute deflector plate
The predicted wear depth distributions and the resulting deformed shape of the plate are shown in Figure 2. It was observed that the abrasive wear is localized in regions where the material flow exerts high pressure on the plate surface, while the erosive wear occurs in regions where the particle impact velocity and frequency are high, or where the impact angle is oblique.
Figure 2 Predicted deflector plate wear using the Archard and Oka models
In this application, the prediction of the wear depth distribution enables the virtual optimization of the deflector plate shape and the chute operational parameters to minimize wear. Furthermore, the introduction of geometry deformation due to wear enables the analysis of deflected particle trajectories as the plate geometry evolves, which can inform the necessary adjustments in the plate inclination angle over time.
It is worth pointing out that, while the results of the Archard and Oka wear models are shown separately here for the purposes of comparing them, the models can be used together to produce the deformed shape due to combined abrasive and erosive wear.
Results such as the ones shown in Figure 2 are difficult and costly to obtain experimentally, making EDEM analysis a valuable addition to the design process. In this context the Oka [2,3] erosive wear model complements the already built-in Archard abrasive wear model [1] to provide a complete wear modeling suite in EDEM, while the recently developed geometry deformation EDEM API method enables a higher fidelity wear modeling, which captures the evolution of equipment shape and the resulting effects on equipment performance.
If you are interested in using our deformable wear models please visit these pages in the Knowledge Base:
Archard Abrasive Wear model with geometry deformation
Oka Erosive Wear model
References
[1] Archard, J.F., (1953). Contact and rubbing of flat surfaces. J. Appl. Phys. 24, 981–988.
[2] Oka, Y. I., Okamura, K., & Yoshida, T. (2005). Practical estimation of erosion damage caused by solid particle impact: Part 1: Effects of impact parameters on a predictive equation. Wear, 259(1–6), 95–101. https://doi.org/10.1016/j.wear.2005.01.039
[3] Oka, Y. I., & Yoshida, T. (2005). Practical estimation of erosion damage caused by solid particle impact: Part 2: Mechanical properties of materials directly associated with erosion damage. Wear, 259(1–6), 102–109. https://doi.org/10.1016/j.wear.2005.01.040