Designing efficient and silent Motor Drives
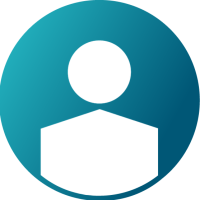

One of the key drivers for electric drives adoption is the high level of efficiency they provide. Thanks to power electronics and digital control, electric drives can be tuned and optimized to improve sustainability and reduce the energy consumption that is required to produce mechanical actions. For electric cars or any other electric vehicle, this is essential as it is directly linked to the range of the vehicle.
The power converter and its control have a direct impact on the electric motor. If these components are designed separately, you may encounter some disappointing behaviors when connecting them for the first time. A detailed understanding into these complex interactions should happen early in the design process with virtual testing to make sure all performance requirements are met. This is not only for the efficiency of the motor drive, but also for observation of temperature rise and possible noise issues.
Simulation technologies can now enable such evaluations, representing in detail each component of the drive and how they interact with each other. It allows for the testing of various situations virtually to avoid late and costly redesigns. When simulating motor drives, what happens very often is components such as the motor and the power converter are represented in a simplified way to ensure convergence and reasonable solving times can be met, which is not ideal for a detailed analysis with multiple design factors at play. Altair solutions enable the use of suboptimal models of power converters and motors, and then captures the impact of various design decisions on the system performance. This is broadly applicable across all motor drives used in electrification for automotive, aerospace, and heavy industry vehicles.
Motor drives can be simulated in Altair® PSIM™, a tool dedicated to power electronics and motor control design. In complement, finite-element based tools like Altair® Flux® and Altair® FluxMotor® can provide reduced-order models of electric machines that can be directly used by PSIM and connected to the rest of the system represented in 1D. High fidelity models can be used for both the motor and the inverter. Key areas of interest are efficiency of the combined motor drive, controllability of the motor, and impact on the developed torque of the machine. The developed torque is of particular interest as spatial harmonic ripple in the torque can be large enough and at low enough frequency to contribute to noise, vibration, and harshness (NVH).
Fig 1: Flux coupled to PSIM to simulate the full motor drive
Let’s take the example of a typical traction machine (Permanent Magnet Synchronous Machine) used in an electric vehicle. Tables are extracted from Flux and then used in PSIM in which we apply PWM (Pulse Width Modulation) control. Using some scripting to vary operating points, it is possible to obtain the efficiency maps of the motor, the inverter, and the whole drive as shown in Figure 1.
Fig. 2: Efficiency maps of the motor alone, the inverter and global motor drive
PSIM simulation also allows users to obtain the current shapes that can be fed back to Flux in order to have a precise evaluation of the losses generated by the harmonic content that is introduced by PWM control. Figure 3 shows the increase in temperature due to increased permanent magnet and winding losses when compared to pure sinusoidal source. It also has an impact on the noise of the machine that we can compute by extracting the forces and performing a vibration analysis.
Fig. 3: Temperature comparison between pure sine supply and PWM.
Understanding the strong interaction between the motor, the inverter, and the control is key to designing an optimal motor drive. Simulations based on high fidelity models can capture various effects and allow for early design decisions.
If you want to learn more about simulation results on this topic, please join our Accelerate E-NNOVATION webinar series on power electronics here.