Breaking ground with the new Tavares breakage model
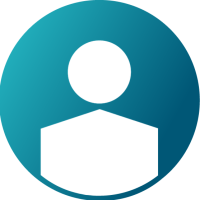
Particle damage and subsequent size reduction is characteristic across a wide range of applications, such as comminution, transportation, materials handling, separation and geotechnical applications. This makes the breakage of materials a hot topic these days with a lot of interest and research around the best methods and models to simulate and predict this complex process.
EDEM (now part of Altair) has been very active over the years on that front and developed a model that was able to describe such phenomena for certain loading conditions. The ultimate goal is to provide a breakage model that will be able to accurately capture the complex breakage mechanisms and provide the fragment size distribution including the fines. After months of intensive development, we are pleased to announce the availability of a new model called ‘Tavares Breakage Model’. This model is based on previous well-established research at the Federal University of Rio de Janeiro (L.M.Tavares et al 2002, 2009, 2012, 2013) and is the result of close collaboration between Prof. L.M.Tavares, Prof. J.Ooi and the EDEM R&D Team. It describes the breakage of brittle materials but most importantly uses an innovative approach for particle replacement that captures accurately the kinematics of the fragments, eliminates mass loss, while keeping a high degree of fidelity in describing the material response.
Figure 1 – Calculation cycle of Particle Weakening and particle replacement due to body breakage
There have been many mathematical models that fail to provide realistic results either because of their premature nature, large number of fitting parameters, great complexity or, most importantly, poor accuracy and excessive computational cost. The new Tavares Breakage Model minimizes the use of fitting parameters, uses contact detection for spheres to achieve computational efficiency and uses a state-of-the-art method to replace the particles with fragments of various sizes. Also, it employs a new stochastic approach that allows representing fragment size distribution with great fidelity down to the fine sizes, contrasting with previous studies that also used spherical particle replacement but that were deterministic in nature.
Over the years there have been different numerical approaches that describe the breakage of materials, but the only viable option that considers the flow of material due to breakage is the Discrete Element Method (DEM). DEM can capture the different modes of particle fracture, hence this method has proven to be a great predictive tool both for milling, crushing and other applications where particles are subject to complex series of loading events.
EDEM software is used by many customers in the mining and mineral processing industries with a need for modelling a number of unit operations. This need has been the driving force for the EDEM team to include a model that will be able to capture both catastrophic breakage (when particles suffer a significant impact) as well as weakening of particles by unsuccessful stressing events. Finally, the new Tavares breakage model delivers the final size distribution of the material including the fines, giving predicted size distributions that extend below the minimum particle size used in the DEM simulation. The implementation of the model has been verified on the basis of the continuum model from L.M. Tavares and A.S. das Chagas (2020) and validated based on single-particle tests and unconfined particle-bed experiments. The results of the latter are being prepared for publication in peer-reviewed journals.
Capturing the fines in your system
EDEM has introduced this new breakage tool which produces the fines resulting from breakage simulations using the new Tavares Breakage model. This is an EDEMpy tool and it is in the form of an executable file that uses Python libraries to post-process the simulation data. It is a smart method that combines computational efficiency, extending the complete size distribution of fragments without the need to create tiny particles within the DEM simulation and accuracy. This allows for faster simulations and realistic results!
In EDEM all breakable particles are being replaced by families of fragments with different size distributions, replicating real-life scenarios. A particular feature of these families is the presence of a special dummy size class, which is included to ensure that no significant mass loss or gain occurs each time a parent particle is replaced by its fragments. The particles that belong in this special dummy size class are not allowed to break further in the simulation and they represent the fines in the system. Therefore, once the simulation is completed and considering the breakage intensity of the event the dummy particles are replaced by the corresponding distribution of the fines.
Complete size distribution including the fines: Comparison of modelled (lines) and simulated (symbols) size distributions from breakage of 28.9 mm copper ore particles at different impact energies. The black dashed line depicts the minimum size that a particle (fragment) can reach after which can no longer break and is considered dummy and the red dashed line represents the user defined minimum global fragment size that can be produced during the simulation (1.5mm).
The Breakage tool is very easy to use and does not require any external software to run apart from the Anaconda distribution of Python. Instructions for this can be found in the installation folder of EDEM under the EDEMpy folder (C:\Program Files\Altair\XXXX\EDEMXXXX).
Just run the script through the command line, define your input parameters and get your results. A ready-made graph appears on the screen which contains the cumulative PSD and the retained mass in the system, as well as the spreadsheet with all the relevant values is exported in the folder. For more information on the tool please refer to the Tutorial.
Outputs in EDEM
The Tavares breakage model provides a list of outputs related to particle breakage due to impact, weakening of particles due to repeated stressing and their related energies, as well as the body breakage and the final size distribution of the fragments and their fines.
The breakage model is currently available as an API and it includes the .dll file, used as an input in the physics section in EDEM, as well as the preference file containing the input parameters of the breakable materials and the FracturePatternDistributions folder. For guidelines on how to setup an example simulation and tips regarding the parameters please refer to the Setup_guidelines and the Tutorial document.
The outputs of the breakage model are the following:
- New fracture energy per particle type
- Fragment size distribution
- Cumulative particle size distribution (PSD) and the retained mass in the system
To download the model and its breakage tool please refer to: https://community.altair.com/csm?id=kb_article_view&sysparm_article=KB0115743&sys_kb_id=3d04af7a1be62450c4dfdbd9dc4bcb39&spa=1
Professor Tavares of the Federal University of Rio de Janeiro commented:
“The model was the result of over a quarter of a century of testing single particles and applying the resulting equations proposed to a number of operations that include different types of mills and crushers, as well as degradation of materials during handling. Its implementation in EDEM was the result of a very successful collaborative effort, and the outcome is a model that allows very realistic predictions, without the high computational cost.”
Professor Ooi of the University of Edinburgh added:
“I am very pleased to have this opportunity to work with Prof. Tavares and the Altair EDEM R&D colleagues to develop this much improved predictive model for milling processes. The model has successfully coupled the strength of EDEM in simulating the particle dynamics during milling with the fracture energies and the fragment size distributions based on robust experimental observations.”
References
Tavares L.M. and King R.P. (2002) Modeling of particle fracture by repeated impacts using continuum damage mechanics. Powder Technology 123(2): p. 138-146.
Tavares L.M. (2009) Analysis of particle fracture by repeated stressing as damage accumulation. Powder Technology 190(3): p. 327-339.
Tavares L.M. and de Carvalho R.M. (2012) Modeling ore degradation during handling using continuum damage mechanics. International Journal of Mineral Processing 112-113: p. 1-6.
de Carvalho R.M. and Tavares L.M. (2013) Predicting the effect of operating and design variables on breakage rates using the mechanistic ball mill model. Minerals Engineering 43-44: p. 91-101.