What's new in Altair FluxMotor 2021 ?
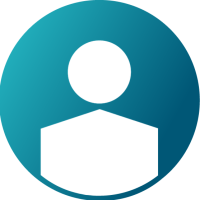

Altair FluxMotorTM 2021 – Highlights
Among the many new capabilities of FluxMotor 2021, a large step forward has been made for thermal analysis which now allows for transient analysis and the computation of temperature variations in time during duty cycles.
The main features of the version are listed below:
- Transient thermal computations in Motor Factory
- Duty cycle with thermal solving
- Model maps defined with thermal solving
- Reluctance synchronous machine, a new available machine, with 10 tests for evaluating performance
- A new way to fill slots with elementary wires has been added to improve winding area
- A model of machines can be exported to Flux 2D with the representation of the solid conductors inside the slot (allowing the computation of winding AC losses)
- NVH prediction for induction machines – inner rotor (in beta mode)
- Additional new features and improvements
For more details …
Transient thermal computations in Motor Factory
“Characterization – Thermal – Motor & Generator – Transient” test is to evaluate the impact of electromagnetic performance on the thermal behavior of the machine in a transient mode for both synchronous machine with permanent magnets – Inner rotor (SMPM-IR) and Induction machine with squirrel cage – Inner rotor (IMSQ-IR).
A thermal working point defined by a speed and a set of losses can be considered to compute the temperature charts and the main thermal parameters. The inputs describing the thermal working point can be set manually or imported from electromagnetic tests that were previously solved.
Synchronous machine with permanent magnets – Inner rotor Characterization – Thermal – Motor & Generator – Transient |
Induction machine with squirrel cage – Inner rotor Characterization – Thermal – Motor & Generator – Transient |
Duty cycle with thermal solving
For a synchronous machine with permanent magnets – Inner rotor (SMPM-IR) the computation of the driving cycle can be done by considering the thermal solving in the framework of the test “Performance mapping – Sine wave – Motor – Efficiency map”.
The duty cycle with a list of working points is characterized by speed and torque. All along the cycle, the physical properties and the control command are updated by considering the temperature variations inside each region of the machine.
Driving cycle with thermal solving |
Model maps defined with thermal solving
In the test “Characterization - Model - Motor - Maps” which gives 2D maps in Jd-Jq plane for characterizing the 3-Phase synchronous machines with permanent magnets, it is now possible to perform thermal computation. This can be done by considering the magnet temperature in a predefined range of temperatures.
Hence, the displayed maps in this test are updated according to the selection of the defined range of magnet temperatures.
Model maps defined with thermal solving |
A new available machine: Reluctance synchronous machine
A new type of machine is now available in FluxMotor with its own design, test, and export environment in Motor Factory. You can run 10 tests to evaluate performance.
A new library has been added to the Part Library. 200 topologies of saliencies and 4 standard motors are stored inside a new catalog of Motor Catalog.
Reluctance synchronous machine – Tests for evaluating the performance |
Reluctance synchronous machine – Part libraries |
Winding area improvement
In the winding area, new sections have been added to help you build the winding step by step: winding architecture, design of the coils, insulation, end-windings, and potting.
In the coil section, in addition to the usual coil composition (turns, wires and dimensions), it is possible to select a method for filling the slot with elementary wires and to group them to shape the conductors. This allows well evaluating the feasibility of the winding (computation of a filling factor very close to the real one).
A new winding area to fill the slots with conductors |
On the other hand, in the "Export" area, the model of the machine can be exported from FluxMotor to Flux 2D with the representation of the solid conductors inside the slot. This will save you a lot of time modeling when you want to make advanced studies in Flux 2D for computing AC losses in winding for instance.
Exported model from FluxMotor to Flux 2D with a representation of the solid conductors |
NVH prediction for induction machines – inner rotor (in beta mode)
These tests allow you to perform a NVH prediction in the early electromagnetic design stage of induction machines with an inner rotor. Note: Only available at the beta user level.
- Computation of sound power level corresponding to a working point characterized by line-line voltage, power supply frequency, and speed (U, f, N)
- Computation of sound power level corresponding to a working point characterized by line current, power supply frequency and speed (I, f, N)
Note: For both tests, the forces on teeth can be computed and displayed. - Spectrogram based on several working points characterized by line-line voltage, power supply frequency, and speed (U, f, N)
- Spectrogram based on several working points characterized by line current, power supply frequency, and speed (I, f, N)
Motor Factory – Mechanics – NVH - Working point (U, f, N) - Sound power level and force on teeth computation |
Motor Factory – Mechanics – NVH - Spectrogram (U,f,N) - Overall sound power level versus speed |
Additional new features and improvements
- New connectors are available for coupling FluxMotor with HyperStudy with a lot of newly developed tests.
- In the test “Characterization – Model – SSFR” dedicated to induction machines with squirrel cage, new advanced user inputs are available to set the linear magnetic permeability to be considered for characterizing the equivalent scheme parameters.
|
Settings of the magnetic permeabilities for the stator, rotor, and shaft |
|
Settings of the magnetic permeabilities for the stator, rotor, shaft Automatic mode (1) or user modes (2) |
- FMU format files that are exported from FluxMotor are now compatible with all kinds of environments, such as Activate and others…
In the EXPORT environment of Motor Factory, the area “FORMAT”, allows you to export data such as constants, curves, and maps in FMU format files.
In the previous version, the exported FMU format files were mainly dedicated to being used in environments like Altair ActivateTM inside block functions, ready to be integrated into schemes to represent the model of the corresponding rotating electrical machine. In the current version, two packages of FMU format files are automatically provided, one dedicated to Activate and another one compatible with other system simulation tools.
Hence, you will be able to select what is needed considering the used system simulation tool without any problem of compatibility. One of the main differences between the two files is how are the units managed in the name labels (See below illustrations).
|
Exported FMU format files dedicated for Activate |
|
Exported FMU format files (Generic) compatible with other system simulation tools |
- New values for allocated memory in user preferences:
- Maximum memory for Motor Factory has been modified. The default value has been increased to 4096 MB and the range of possible value goes up to 8192 MB
- Default allocated memories for Flux2D and Flux Skew have been modified respectively 4196 MB and 8192 MB. Moreover, the dynamic memory of Flux2D and Flux Skew can be selected as well.
- Maximum memory for Motor Factory has been modified. The default value has been increased to 4096 MB and the range of possible value goes up to 8192 MB