Calculated vs Simulated Weld Stress Results
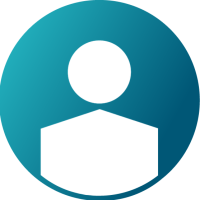
I'm analyzing a crane design. The FEA results do not match up with the analytical calculations. For example, when analyzing this connection between a piston and a post:
I assumed this weld pattern:
with the welds being 9 mm fillets.
The connection is loaded vertically, with the load being offset from the weld pattern:
I calculated the primary and secondary shear stresses on the weld pattern and found the max stress (at the top/bottom of the weld pattern) to be 3.4 MPa.
I assumed a E60xx weld electrode with a yield strength of 345 MPa. I assumed a shear yield strength of 50%. My calculated load factor was therefore 50.
I then simulated the structure and found stress values that were an order of magnitude larger than calculated:
I isolated a small section around the connection and simulated it with the backplate (section of the post) fixed at the edges:
I simulated the section again, but constrained the entire face of the backplate. The stresses again dropped by 50% but were still much larger than calculated:
After mesh refinement, the large stress value is concentrated in the corner(s). The stress values adjacent to the corner are closer to the calculated values, but still higher:
What am I doing wrong and/or how do I reconcile the discrepancy between the calculated and simulated results?
Thanks.
Answers
-
I believe you're evaluating a singularity region in there, and the more you refine, the worse it will get.
Please, consider using the embed Wled fatigue modeling in OS, as mentioned in your other post.
https://community.altair.com/community?id=community_question&sys_id=34889470db7e1510cfd5f6a4e2961922
0