Weld stress simulation
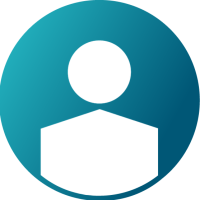
I am analyzing weld stresses during vibration for fatigue. I extract the absolute max principal stress ranges, and then refer to a standard to check if the stress ranges are acceptable for fatigue life.
The mesh consists of shell elements:
When modeling fillet welds, I set the weld size to half the actual weld size, to simulate a mid-surface. I set the weld elements thickness to the effective throat size:
The weld is modeled using multiple elements, instead of a single element, which I see in the Altair reference material.
The nodes of the parent component elements are not equivalenced, so the load is carried only via the weld. I see that Hyperlife (which I don't know how to use yet) requires that the parent component nodes be equivalenced and the weld not modeled at all. I've found that when I forget to detach the parent material elements from each other, the stress results are greatly reduced. My understanding is that this is because equivalenced nodes simulate a complete joint penetration weld rather than a fillet weld.
My results show a relatively large tensile stress (for fatigue life) in the weld elements. I'll get lower values if I mesh the weld using a single element for the weld, so I'm not comfortable meshing the weld with only 1 element:
My questions are:
1. Is this the correct method for modeling the welds?
2. Should I be considering the stress values in the weld itself? Or ignoring those and considering the results in the parent materials at the weld interface?
Answers
-
If I recall correctly, when you run weld fatigue analysis in OptiStruct, it uses Volvo method for calculating the hot spot stress values at the weld toe, and not the direct stress values from the weld elements. So I would say, 1 element row is fine for your modeling if you're using the implemented method.
Take a look at the solver Help User Guide for Fatigue Analysis.
0