Results overestimating stress & displacement
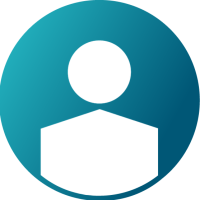
I've modeled a rectangular tube being clamped via a pretensioned bolt:
The tube is 10 mm thick (steel) and is fixed at one end. The pretension force is 50 kN.
I also modeled a 50 kN nodally-distributed force on the washers of another connection, to compare the results:
The contacts between the components are set to "friction" with a coefficient of 0.7:
The simulation is a non-linear static analysis.
The stress results are very large. Especially around the hole edge:
I realize that 660 MPa is an overestimation as the stress is beyond the yield stress. But these results suggest yielding around the hole.
Additionally, the deformation results show a deformation of 0.2 mm at the hole edge:
However, just from experience/intuition, it is obvious that torquing a bolt to spec (50 kN clamp load) will not cause a 10 mm thick tube to yield.
I had a test done. After torquing the bolt 50 kN, the bolt deflected 0.1 mm (not 0.2 mm as predicted by the simulation). Upon release, the tube sprang back with no evidence of plastic deformation.
What is going on? What am I doing wrong?
Answers
-
Can you share the model? From your pictures I'm not sure exactly how you have set up the connections between bolts and parts and washers with RBE2 etc, Part of the issue might be that the shells can't compress through their thickness?
Also, do you know you are definitely getting to 50kN in the physical bolt? Did it have a loadcell? Or are you relying on the torque measurement to map to a tensile force?
0 -
Paul Sharp_21301 said:
Can you share the model? From your pictures I'm not sure exactly how you have set up the connections between bolts and parts and washers with RBE2 etc, Part of the issue might be that the shells can't compress through their thickness?
Also, do you know you are definitely getting to 50kN in the physical bolt? Did it have a loadcell? Or are you relying on the torque measurement to map to a tensile force?
Hi Paul,
I've attached the model. In the model, the tube is clamped between a flat bar and a channel, with washers on both ends of the bolt. In the test, it was just the bolt head and the nut clamping the tube. That should make it even worse.
I can't be certain that the bolt is tensioned at 50 kN. I'm relying on the conversion from the applied torque.
Thanks.
0 -
AM_20700 said:
Hi Paul,
I've attached the model. In the model, the tube is clamped between a flat bar and a channel, with washers on both ends of the bolt. In the test, it was just the bolt head and the nut clamping the tube. That should make it even worse.
I can't be certain that the bolt is tensioned at 50 kN. I'm relying on the conversion from the applied torque.
Thanks.
Apologies, I was on vacation most of this week, I took a look, and I think it is ok with a couple of small modifications, in your original, your washers are barely bigger than the hole on their OD, and you only have contact across a single element, just increasing the washer size and contact area brings the stress down a bit.
I added simple MATS1 non linear material and ran as shells and also solids, you can see the plastification is very low (percentage wise) at hole edge only, so it wouldn't give visible permanent set in the overall displacement (as you suggest from physical test)
I attached revised shell and solid models for you to take a look
0 -
Paul Sharp_21301 said:
Apologies, I was on vacation most of this week, I took a look, and I think it is ok with a couple of small modifications, in your original, your washers are barely bigger than the hole on their OD, and you only have contact across a single element, just increasing the washer size and contact area brings the stress down a bit.
I added simple MATS1 non linear material and ran as shells and also solids, you can see the plastification is very low (percentage wise) at hole edge only, so it wouldn't give visible permanent set in the overall displacement (as you suggest from physical test)
I attached revised shell and solid models for you to take a look
Thank you very much.
0 -
Paul Sharp_21301 said:
Apologies, I was on vacation most of this week, I took a look, and I think it is ok with a couple of small modifications, in your original, your washers are barely bigger than the hole on their OD, and you only have contact across a single element, just increasing the washer size and contact area brings the stress down a bit.
I added simple MATS1 non linear material and ran as shells and also solids, you can see the plastification is very low (percentage wise) at hole edge only, so it wouldn't give visible permanent set in the overall displacement (as you suggest from physical test)
I attached revised shell and solid models for you to take a look
Hi Paul,
Thanks for your help.
Where did the MATS1 H value of 30000 come from?
I need help interpreting these results.
Both the linear and non-linear simulations show me that the stress is beyond yielding around the hole. So I know there is plastic deformation in that region.
Is there an advantage in this case in running a non-linear simulation (or can MATS1 only be run in NL)?
The plastic strain is indeed very small and the max VM stress is 285 MPa, which is below the ultimate strength. Can I conclude from this that the edge of the hole will experience plastic deformation (a very small amount), but that there will be no failure at that location?
Also, why is there such a large discrepancy between the stress in the solid model vs the shell model?
0