Very trivial: Building a mechanism from the ground up
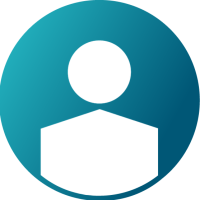
Hello,
While this is probably as trivial as it gets, I still have to ask since the e-learning video just is not helpful with it having you preload a set up file.
I am switching from Solidworks' MBS-suite/ADAMS View (undergrad at university, mind the lack of/miniscule amount of experience on my part) to MotionView and find it hard to get an initial grip on how the setup for a basic mechanism works.
My situation is the following: I want to stand up a very simple model with which I would be able to sway a beam (top view) mounted on a revolute joint ("joint 1")that is "floating in thin air", to which a disk from a disk plough is mounted (also with a revolute joint, "joint 2").
I find myself describing how I am going at it, but after rewriting it for the third time I realize that something as trivial as combing two bodies with two joints does not need that.
What is Motionviews equivalent of importing a beam-part and a revolutejoint-part into Solidworks, fixing the joint into thin air, and mounting the swaybar and the "joint-2" mounted disc?
I apologize in advance if this truly is that simplistic, but I have set up Scissor lifts in Solidworks Motion and ADAMS and have not found myself struggling like this.
Best Answer
-
Hi Gentrit,
From what I can tell, you will have 2 bodies in this model, a Beam and a Disk. The Beam is constrained on one end to Ground by a revolute joint. The Disk is constrained to the Beam at a point, somewhere in the middle, by a revolute joint as well. It looks like you also want the Disk to be constrained such that it will be parallel to the dotted axis in your picture. To add this third constraint, you could add a primitive joint such as a parallel axes joint. To move the Beam, I used a Motion on the revolute joint that connects the Beam to Ground.
I have mocked up an example model that I believe captures what you are describing. Please find it attached. Hopefully this clears up what difficulty you were having in your attempted model.
Hope this helps!
Adam Reid
1
Answers
-
Hi Gentrit,
From what I can tell, you will have 2 bodies in this model, a Beam and a Disk. The Beam is constrained on one end to Ground by a revolute joint. The Disk is constrained to the Beam at a point, somewhere in the middle, by a revolute joint as well. It looks like you also want the Disk to be constrained such that it will be parallel to the dotted axis in your picture. To add this third constraint, you could add a primitive joint such as a parallel axes joint. To move the Beam, I used a Motion on the revolute joint that connects the Beam to Ground.
I have mocked up an example model that I believe captures what you are describing. Please find it attached. Hopefully this clears up what difficulty you were having in your attempted model.
Hope this helps!
Adam Reid
1 -
Hi Adam, thanks a lot for your reply and time, excuse my timing as I am sitting across the pond.
Yes, your model does represent my idea, only now do I get why this initial joint wouldn't work: The beam I made by using a cylindergraphic had no body assigned to it and creating a Joint between the imported Disc and the bodyless beam graphic led to me connecting the ground body to itself which of course makes no sense. Looks like any graphic which you have not explicitly assigned a body to yourself gets the ground body assigned to it by the program.
I have been tinkering around with your model and am left with the following questions:
In Solidworks' Motion Analysis equivalent I, for example, would import a metal sheet with a slot hole and a corresponding bolt. I would use the "Mate"-feature which would have me pick these two parts and ask whether I want to create a corresponding joint: they would mostly align, I then would add distance constraints et cetera to create the intended joint. Here, I use the "Joints"-feature which has me pick the two parts and a point on which the joint is located. The parts themselves do not get aligned in any way, they stay in place without any relative parameters to define. (This seems to be the same approach as in ADAMS View, however I never used any geometry beyond simple links there, so I cannot make that mental bridge here) How do I define a proper position for a joint? Do i need to use explicit geometry for that, or can I just use distances/axes along which I would later design steel beams?
How do I make sure the disc, while the beam is swaying around, remains either parallel to the global, say, XZ-Plane, or keeps a certain angle towards that plane? Can I place "probes" that would record the values of different angles during the motion, to which I could then refer to for a plot in the post processor? I see the parallel axis joint and the marker that you created, but dont understand how you used them. The Disc also seems to be some annoying geometry to deal with as there is not a whole lot of geometry to snap to or refer to for a reference plane. Perhaps markers are a solution?
(I am sure if I had some colleague present who uses MotionView, he would have been able to show me in less than 5 minutes, all while I am expressing my confusion. I hope I am not being too complicated to deal with
)
0 -
Gentrit Krasniqi said:
Hi Adam, thanks a lot for your reply and time, excuse my timing as I am sitting across the pond.
Yes, your model does represent my idea, only now do I get why this initial joint wouldn't work: The beam I made by using a cylindergraphic had no body assigned to it and creating a Joint between the imported Disc and the bodyless beam graphic led to me connecting the ground body to itself which of course makes no sense. Looks like any graphic which you have not explicitly assigned a body to yourself gets the ground body assigned to it by the program.
I have been tinkering around with your model and am left with the following questions:
In Solidworks' Motion Analysis equivalent I, for example, would import a metal sheet with a slot hole and a corresponding bolt. I would use the "Mate"-feature which would have me pick these two parts and ask whether I want to create a corresponding joint: they would mostly align, I then would add distance constraints et cetera to create the intended joint. Here, I use the "Joints"-feature which has me pick the two parts and a point on which the joint is located. The parts themselves do not get aligned in any way, they stay in place without any relative parameters to define. (This seems to be the same approach as in ADAMS View, however I never used any geometry beyond simple links there, so I cannot make that mental bridge here) How do I define a proper position for a joint? Do i need to use explicit geometry for that, or can I just use distances/axes along which I would later design steel beams?
How do I make sure the disc, while the beam is swaying around, remains either parallel to the global, say, XZ-Plane, or keeps a certain angle towards that plane? Can I place "probes" that would record the values of different angles during the motion, to which I could then refer to for a plot in the post processor? I see the parallel axis joint and the marker that you created, but dont understand how you used them. The Disc also seems to be some annoying geometry to deal with as there is not a whole lot of geometry to snap to or refer to for a reference plane. Perhaps markers are a solution?
(I am sure if I had some colleague present who uses MotionView, he would have been able to show me in less than 5 minutes, all while I am expressing my confusion. I hope I am not being too complicated to deal with
)
Hi Gentrit,
For repositioning the CAD, your workflow would look like the following:
- Create a body for each component, the sheet and the bolt.
- Create a graphic to attach to each body, either with CAD or primitive shapes.
- Create a point where the joint is to be located
- Create a joint with the sheet (body 1), bolt (body 2), at the specified point.
- For alignment of the bolt CAD, you can use the Move Tool (top left of the ribbon) to relocate the bolt graphic to a certain position. This can be done by picking a point on the CAD graphic and then dragging it to a snap point, or by typing in the transform coordinates.
As for the joints, they are simple constraints that you apply to bodies to restrict certain degrees of freedom. These are common joint types and there is plenty of documentation available either online or in our help files. The parallel axis primitive joint simply removes a single degree of freedom, in that case rotation about the X axis, which is what keeps it parallel to the Z axis. The joint you likely would use in your case is the planar joint, which removes displacement in one direction and rotation in one direction. This would make the disk only able to move along the YZ plane in the model I provided and not able to rotate in the Y axis. Obviously, that plane can be set to any you need.
With respect to 'probes', these are called Outputs. You can use the guide bar to easily create Outputs for displacement, velocity, acceleration, force, custom expressions, or custom user subroutines. In your case, you would create an Output for angular displacement between two bodies and then review that in the HyperGraph post-processor.
As a reminder, we do have a comprehensive eLearning course MotionView/MotionSolve Introduction v2023 eLearning that can help you learn these introductory topics at your own pace.
Hope this helps!
Adam Reid
0 -
Hi Adam,
With the help I managed to set the model up how I was imagining it, however I can not find the mentioned option for setting up an Output that measures angular displacement between bodies/features in general. How would you go about for setting that up? Velocity, Acceleration and Force obviously are no option; "Expressions" and "User Defined" have you pick a body after which nothing seems to happen or some faulty output is being created. "Displacement" does not offer an angular measurement between two vectors, surfaces or else, so I don't see how the provided options can be used.
Do I have to use the expression builder? In that case, choosing the expression option from outputs (on v2022.3) does not give me access to the expression builder window popping up like it is described here.
0 -
Gentrit Krasniqi said:
Hi Adam,
With the help I managed to set the model up how I was imagining it, however I can not find the mentioned option for setting up an Output that measures angular displacement between bodies/features in general. How would you go about for setting that up? Velocity, Acceleration and Force obviously are no option; "Expressions" and "User Defined" have you pick a body after which nothing seems to happen or some faulty output is being created. "Displacement" does not offer an angular measurement between two vectors, surfaces or else, so I don't see how the provided options can be used.
Do I have to use the expression builder? In that case, choosing the expression option from outputs (on v2022.3) does not give me access to the expression builder window popping up like it is described here.
Hi Gentrit,
When you click the Outputs icon (
) you should then see the context-relevant Guide Bar:
If you were interested in measuring the displacement of a joint, for example, you would change the option from Two Points to Entity and then choose the type as Joint:
This will create X, Y, Z, and MAG outputs for both translational and rotational displacements. If you want to use a different reference frame than the Global Frame, such as a marker on an existing Body instead to see the relative displacement, you can change that marker any time.
The expression-based Outputs are very useful when you have something very particular to measure and the generic Outputs just wont capture it. In that case, you would create an expression of the angular displacement you want. For example, if there existed a marker (m_1) on body 1 and another marker (m_2) on body 2, and you wanted to track the angular displacement about the X axis between marker 1 and marker 2 relative to marker 1, the expression would look like:
`AX({m_1.idstring},{m_2.idstring},{m_1.idstring})`
https://help.altair.com/hwsolvers/ms/topics/solvers/ms/ax.htm
Hope this helps!
Adam Reid
1