stress results comparison
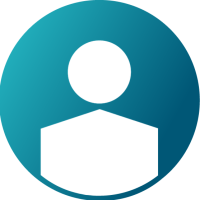
Hello all.
I know there is a very good tutorial on the subject (https://www.youtube.com/watch?v=236ofmwz1X4) however I would like to share my latest experience when comparing stress results obtained from two different solvers i.e. MSC NASTRAN and Optistruct. By default NASTRAN calculates stress using the command: STRESS(PLOT,SORT1,REAL,VONMISES,BILIN)=ALL, meaning that (if you neglect the other terms) a bilinear extrapolation is used to get the stresses from the element's centroid to the nodes.
Since optistruct/RADIOSS calculates stress at the element's centroid by default, I supposed that the equivalent command in the .fem input file for optistruct would be: STRESS(SORT1,H3D,REAL,ALL,BILIN) = YES (I have replaced 'VONMISES' with 'ALL' to have all stresses in my output) and performed two examples of simple static analyses: one with shell elements: the well known hole in plate and another with a bracket meshed with solid elements (4 noded tetras). In both cases the results from MSC NASTRAN and Optistruct were identical, as long as in Hyperview I activated the option 'use corner data' (participation of element to the node). Without 'corner data' activation the difference in VM stress between NASTRAN and Optistruct for the hole in plate problem was 175 MPa (NASTRAN) to 157 MPa (Optistruct).
Now: I performed an analysis of a 3d bolted connection (two plates connected with a 3d bolt) with bolt pretension as a first step and a tensile force acting on the top plate of the connection as the second step. Obviously, this problem involved contact between the plates and the bolt. The analysis converged and the results were correct since I knew from published results (and NASTRAN) that max. stress should be approx. 80 MPa. I received the same results with optistruct, but without the 'use corner data' activated, although I have used the command described before for stress. If I activate the corner data in Hyperview, then my stresses almost double in magnitude (156 MPa). So, this contradicts with what I have found with my previous tests (hole in plate and 3d bracket). Does it have to do with the 'contact'?
Thank you in advance for your reply.
<?xml version="1.0" encoding="UTF-8"?>
<?xml version="1.0" encoding="UTF-8"?>
<?xml version="1.0" encoding="UTF-8"?>
<?xml version="1.0" encoding="UTF-8"?>
Answers
-
Which verion of OptiStruct you are using? Could you please share the .out file of the run?
0 -
Sure: Optistruct 2018 (student version). I've placed the input file in your dropbox.
Thank you.
0