Optistruct stress result about use corner data option trun on or not
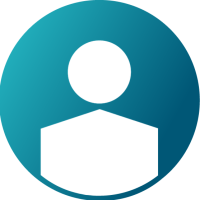
hi,i am new user for optistruct solver
i have some question(plastic) for the result of optistruct analysis.
my material card use mats1(give the two point "one is yield point and the other is ultimate point" form the curve)
i solve a engineer problem,but when i check the result and i confused.
i know the meaning of hyperview option of "use corner data".
turn on the option mean watch the "node vonMises stress"
turn off the option mean watch the "element center vonMises stress"
my question here
if turn on the option and my vonMises stress result will greater than ultimate strength.
if turn off the option and my vonMises stress result will less than ultimate strength and greater than yield strength.
1.If i want to compare vonMises stress between my result and matweb value.(should i turn on or turn off "use corner data")
2.Optistruct plastic curve should input engineering stress-strain or true stress-strain?
3.By the way,matweb stress is Engineering Stress value or True Stress value?
i really need my qeestion answer,and i seach lots of data but i confused.
so if you are a senior cae engineer,can you take a little time to help me,tks
Best Answer
-
tonychen said:
hi senior enigneering ,
the optino of corner data(on/off) ,your percentage(10992.9 and 11589.4) is 5%
so i also do a example but my percentage is very large ,i check very time ,but i can't find mistake,can you help check my fem,thanks
my percentage is 32%(i am crying now)
i ready want to know the differenc between us......
These results are what you would expect, In bending, the highest stress is at the surface, the closer you measure the stress to the surface, the higher it will be, so the corner values at the surface are higher than the centroid, but of the 8 corner values, 4 are lower than the centroidal stress (because they are closer to neutral axis), and 4 higher (further away from neutral axis) as expected
If we take averages of the corner nodes and plot stress through thickness, you can see the stress varies through the thickness, the centroidal stress is in keeping
1
Answers
-
It sounds like you have a reasonable understanding already, the corner stresses (extrapolated from elemental using CORNER, BILIN, CUBIC, GAUSS or SGAGE) will often be higher than centroidal stress values. Reducing element size should reduce the difference between the 2, but isn't necessarily required.
For material data, there may be exceptions, but in general. The stress/strain information in public databases is likely/often derived/calculated from a force/displacement tensile test, the stress is theoretical based on the Force vs Displacement and the cross section of the test coupon (not 'measured' locally in any way, there are only limited ways this could be done) so the stress to compare to if you are modelling a tensile test is likely closer to the centroidal values in Optistruct.
Also, because of this test method, usually the stress/strain curves obtained for a material from a database will be engineering stress/strain. Input stress/strain curves in OptiStruct should be in True stress/strain, but for small displacement models, there is not so much difference between engineering and true stress/strain. So either is ok.
0 -
Paul Sharp_21301 said:
It sounds like you have a reasonable understanding already, the corner stresses (extrapolated from elemental using CORNER, BILIN, CUBIC, GAUSS or SGAGE) will often be higher than centroidal stress values. Reducing element size should reduce the difference between the 2, but isn't necessarily required.
For material data, there may be exceptions, but in general. The stress/strain information in public databases is likely/often derived/calculated from a force/displacement tensile test, the stress is theoretical based on the Force vs Displacement and the cross section of the test coupon (not 'measured' locally in any way, there are only limited ways this could be done) so the stress to compare to if you are modelling a tensile test is likely closer to the centroidal values in Optistruct.
Also, because of this test method, usually the stress/strain curves obtained for a material from a database will be engineering stress/strain. Input stress/strain curves in OptiStruct should be in True stress/strain, but for small displacement models, there is not so much difference between engineering and true stress/strain. So either is ok.
First, thank you for your prompt reply
It sounds like you have a reasonable understanding already, the corner stresses (extrapolated from elemental using CORNER, BILIN, CUBIC, GAUSS or SGAGE) will often be higher than centroidal stress values. Reducing element size should reduce the difference between the 2, but isn't necessarily required.
yes, i had done reduced element size but it fail to reduced stress value.
But i ready need know open the option of use corner data or not?
For material data, there may be exceptions, but in general. The stress/strain information in public databases is likely/often derived/calculated from a force/displacement tensile test, the stress is theoretical based on the Force vs Displacement and the cross section of the test coupon (not 'measured' locally in any way, there are only limited ways this could be done) so the stress to compare to if you are modelling a tensile test is likely closer to the centroidal values in Optistruct.
i understand,tks.
Also, because of this test method, usually the stress/strain curves obtained for a material from a database will be engineering stress/strain. Input stress/strain curves in OptiStruct should be in True stress/strain, but for small displacement models, there is not so much difference between engineering and true stress/strain. So either is ok.
i understand,tks.
0 -
tonychen said:
First, thank you for your prompt reply
It sounds like you have a reasonable understanding already, the corner stresses (extrapolated from elemental using CORNER, BILIN, CUBIC, GAUSS or SGAGE) will often be higher than centroidal stress values. Reducing element size should reduce the difference between the 2, but isn't necessarily required.
yes, i had done reduced element size but it fail to reduced stress value.
But i ready need know open the option of use corner data or not?
For material data, there may be exceptions, but in general. The stress/strain information in public databases is likely/often derived/calculated from a force/displacement tensile test, the stress is theoretical based on the Force vs Displacement and the cross section of the test coupon (not 'measured' locally in any way, there are only limited ways this could be done) so the stress to compare to if you are modelling a tensile test is likely closer to the centroidal values in Optistruct.
i understand,tks.
Also, because of this test method, usually the stress/strain curves obtained for a material from a database will be engineering stress/strain. Input stress/strain curves in OptiStruct should be in True stress/strain, but for small displacement models, there is not so much difference between engineering and true stress/strain. So either is ok.
i understand,tks.
As you decrease mesh size the corner stress shouldn't come down significantly, rather the centroidal stress should go up and get closer to the corner value.
As for which you use, either or both, it depends on the application. Corner data will give higher values at part edges and constraints etc. Depending on the industry you are working in there may be design codes for assessing the stress a certain distance from a constraint. In linear analysis the stress at a rigid constraint will increase the closer you get to it and the smaller you make the mesh.
0 -
Paul Sharp_21301 said:
As you decrease mesh size the corner stress shouldn't come down significantly, rather the centroidal stress should go up and get closer to the corner value.
As for which you use, either or both, it depends on the application. Corner data will give higher values at part edges and constraints etc. Depending on the industry you are working in there may be design codes for assessing the stress a certain distance from a constraint. In linear analysis the stress at a rigid constraint will increase the closer you get to it and the smaller you make the mesh.
I made a small illustrative example, same plate geometry loaded same way (stretched plate with hole), mesh size decreasing, at hole edge, element centroid, stress is 8569 (coarsest) to 10956 (smallest)
but if we look at corner values instead max stress only varies from 10801 - 11304 on same mesh at same location
so for even a very coarse mesh, corner data is close to the centroidal value found on the smallest mesh, and throughout, the smaller the mesh, the smaller the difference between centroidal and corner
0 -
Paul Sharp_21301 said:
I made a small illustrative example, same plate geometry loaded same way (stretched plate with hole), mesh size decreasing, at hole edge, element centroid, stress is 8569 (coarsest) to 10956 (smallest)
but if we look at corner values instead max stress only varies from 10801 - 11304 on same mesh at same location
so for even a very coarse mesh, corner data is close to the centroidal value found on the smallest mesh, and throughout, the smaller the mesh, the smaller the difference between centroidal and corner
thanks a lot
0 -
Paul Sharp_21301 said:
I made a small illustrative example, same plate geometry loaded same way (stretched plate with hole), mesh size decreasing, at hole edge, element centroid, stress is 8569 (coarsest) to 10956 (smallest)
but if we look at corner values instead max stress only varies from 10801 - 11304 on same mesh at same location
so for even a very coarse mesh, corner data is close to the centroidal value found on the smallest mesh, and throughout, the smaller the mesh, the smaller the difference between centroidal and corner
hi senior enigneering ,
the optino of corner data(on/off) ,your percentage(10992.9 and 11589.4) is 5%
so i also do a example but my percentage is very large ,i check very time ,but i can't find mistake,can you help check my fem,thanks
my percentage is 32%(i am crying now)
i ready want to know the differenc between us......
0 -
tonychen said:
hi senior enigneering ,
the optino of corner data(on/off) ,your percentage(10992.9 and 11589.4) is 5%
so i also do a example but my percentage is very large ,i check very time ,but i can't find mistake,can you help check my fem,thanks
my percentage is 32%(i am crying now)
i ready want to know the differenc between us......
These results are what you would expect, In bending, the highest stress is at the surface, the closer you measure the stress to the surface, the higher it will be, so the corner values at the surface are higher than the centroid, but of the 8 corner values, 4 are lower than the centroidal stress (because they are closer to neutral axis), and 4 higher (further away from neutral axis) as expected
If we take averages of the corner nodes and plot stress through thickness, you can see the stress varies through the thickness, the centroidal stress is in keeping
1 -
Paul Sharp_21301 said:
These results are what you would expect, In bending, the highest stress is at the surface, the closer you measure the stress to the surface, the higher it will be, so the corner values at the surface are higher than the centroid, but of the 8 corner values, 4 are lower than the centroidal stress (because they are closer to neutral axis), and 4 higher (further away from neutral axis) as expected
If we take averages of the corner nodes and plot stress through thickness, you can see the stress varies through the thickness, the centroidal stress is in keeping
Hi bro,
i have to say something for you,
you ready save me
i love you!!!!!!!!
i know the answer!!!!
thanks
0