Fatigue analysis SN method, damage/stress interpretation
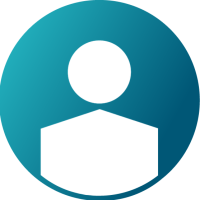
Good morning Altair community.
I need your help regarding the fatigue analysis of this component, a notched aluminum alloy sample (see attached image).
The sample is subjected to a bending force, the load time history is in figure, with R = 0.1, frequency 5Hz.
From experimental tests, I obtained useful data material fatigue properties (in as-build conditions).
SN curve material properties:
"slope-intercept_1segm", Rm = 414MPa, Rs = 232MPa, SR1 = 1073, b1 = -0.17, NC1 = 2e + 06, FL = 90MPa.
Due to bending direction, the top of the sample is expected to be in compression and the bottom in tension. In fact, from fatigue tests, failure occurs on the underside.
However, from the fatigue simulation the contour shows high damage on notched side and limited damage on flat side, different from what expected and verified.
What could be the cause of that? Did I set something wrong?
Second question: with real values SR1, b1, NC1, FL (matfat parameters), do I have to enter specific values in the PFAT card, like surface finish, treatment real, KF, or do I leave them by default?
Third question: in addition to the damage / life outputs, is there a way to obtain other outputs, such as mean stress, etc.?
Many thanks in advance for your help.
Thomas
Answers
-
1) looks like your mesh in the notched area if finer than the flat area. This might affect your results in stress, and also in fatigue. As you're insterested in superficial stress, larger elements might lead to a different reading on stresses on both sides.
2) There are deafault values but for a correlation study you should enter the values/options according to what better fits your testing.
3) i don't know for sure.
0 -
Adriano A. Koga_21884 said:
1) looks like your mesh in the notched area if finer than the flat area. This might affect your results in stress, and also in fatigue. As you're insterested in superficial stress, larger elements might lead to a different reading on stresses on both sides.
2) There are deafault values but for a correlation study you should enter the values/options according to what better fits your testing.
3) i don't know for sure.
1) initially, the goal was to evaluate stresses in the vicinity of the notch, that's why mesh is finer.
I'll try to modify and see what happens. However, I think results will not change, damage values are too much greater in notched side than flat side.
2) I understood your answer. That's what I tried to do at the beginning: I set a common aluminum alloy as a material in the "SN material properties" field in the "fatigue process manager", then estimate from UTS the SN curve. Next step was to change the parameters to correlate the model with the test results. However, knowing the real fatigue behavior of the material (with the related parameters), I entered these values directly (SR1, b1, NC1, FL). But real SN curve already implicitly considers the initially conditions of the specimen (surface finish, surface treatment, ecc).So I was wondering if I should leave default values or not.
Thanks Adriano for your help,
Thomas0